April was the 10th anniversary of the Rana Plaza disaster that reshaped the way we oversee suppliers. If you don’t remember the details, here’s a recap.
Rana Plaza in Dhaka, Bangladesh, was a 4-story building housing retail shops on the street level and 3 stories of sewing factories above that. Sewing workers earned about $1 per day and many supported entire families on this meager wage. Brands such as JC Penny, Benetton, Carrefour, Zara, and others had production in the Rana Plaza building.
One morning in April 2013, the workers on the upper floors noticed cracks in the concrete walls that seemed to be getting bigger. The workers told their supervisors they were frightened by these cracks and were subsequently sent home for the day, while the building was inspected. But the workers were also instructed to come back to work in the morning and threatened with suspension without pay for a month, or they would be fired.
The next morning the workers, desperate to keep their jobs and meager pay, came back and at about 10 a.m. local time, the building collapsed, killing 1,134 people and injuring over 2500.
Reportedly, many of the brand companies using the sewing factories in Rana Plaza had conducted visits and periodic audits of the factories for a few years prior to the collapse. But clearly, these checklist reviews and the results of these audits had not forced sufficient changes to the working environment by the factory operators. Some of the audits reportedly were no more than a simple checklist that did not even include checking fire extinguishers or exit doors.
The lesson to be learned from Rana Plaza and other subsequent supply chain disasters such as the 2015 port explosion in Tianjin, China (death toll 104), the 1911 Triangle Shirtwaist Factory fire in New York City (death toll 146) and other disasters, is that there is no substitute for careful oversight of global supply chain operations and facilities.
Of course, accidents are bound to happen from time to time, but supply chain professionals must learn to be more observant and outspoken regarding their oversight of suppliers and logistics providers, to avoid or mitigate these accidents. For example, when touring a factory, ask about exit routes and signs for emergencies. Observe the condition of the buildings and how they are maintained. Ask about the storage of chemicals and what standards are being followed. Observe the workers and their workstations. Ask about breaks when workers can stretch and use the restroom. While these are cursory observations, they may detect a problem in the making.
We cannot know all of the regulations and building codes in foreign locations, but we can use common sense and ask common sense questions about our supply chain partners.
Most companies have an assigned person or team to address foreign working conditions, safety, environmental concerns, and audit suppliers. You can assist by alerting your internal audit people about your observations and concerns. Coordinate your supplier visits with the auditors and keep each other informed. If your company does not have such a team, there are for-hire audit companies that can do this work.
Take responsibility for checking your supplier’s operations. You may save lives.
About the author:
Rosemary Coates is the Executive Director of the Reshoring Institute and the president of Blue Silk Consulting, a Global Supply Chain consulting firm. She is a best-selling author of 42 Rules for Sourcing and Manufacturing in China and Legal Blacksmith - How to Avoid and Defend Supply Chain Disputes Ms. Coates lives in Silicon Valley and has worked with over 80 clients worldwide. She is also an expert witness for legal cases involving global supply chain matters. She is passionate about reshoring.
SC
MR
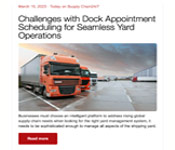
Latest Supply Chain News
- Few executives believe their supply chains can respond quickly to disruptions
- Technology’s role in mending supply chain fragility after recent disruptions
- Tech investments bring revenue increases, survey finds
- Survey reveals strategies for addressing supply chain, logistics labor shortages
- Israel, Ukraine aid package to increase pressure on aerospace and defense supply chains
- More News
Latest Podcast
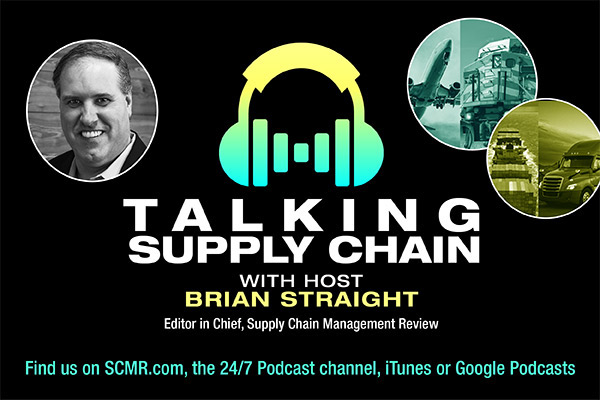
Explore
Procurement & Sourcing News
- Israel, Ukraine aid package to increase pressure on aerospace and defense supply chains
- How CPG brands can deliver on supplier diversity promises
- How S&OP provides the answer to in-demand products
- There is still work to do to achieve supply chain stability
- Blooming success: The vital role of S&OE in nurturing global supply chains
- How one small part held up shipments of thousands of autos
- More Procurement & Sourcing
Latest Procurement & Sourcing Resources
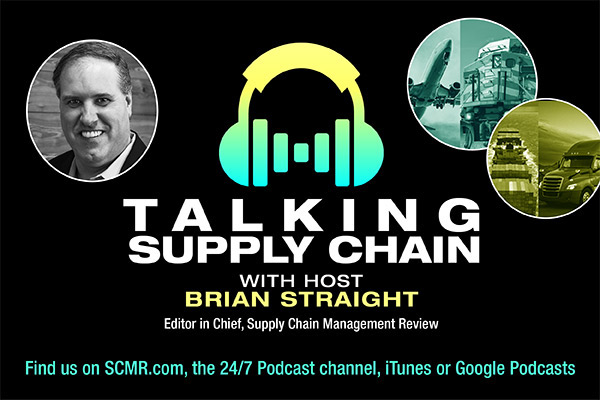
Subscribe
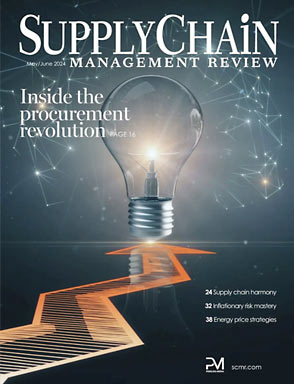
Supply Chain Management Review delivers the best industry content.
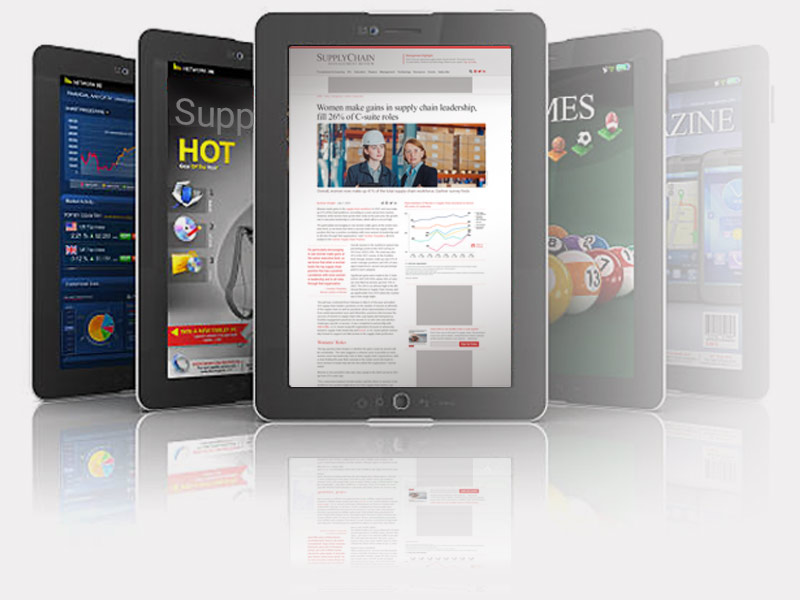
Editors’ Picks



