While the United States warehousing market currently has quite a bit working in its favor in the form of things like tight vacancy rates, strong absorption rates, and rent levels, in some ways it is also a victim of its own success, due to the ongoing strength of e-commerce.
That was one of the main takeaways from a report from commercial real estate firm CBRE, which observes that a high percentage of U.S. warehouse inventory is outdated and not properly equipped to meet the needs and demands that e-commerce activity requires.
CBRE's report, entitled, “Old Storage: Warehouse Modernization in Early Stages” stated that the aging U.S. warehouse inventory does not meet the needs of today's logistics tenants and is creating new development opportunities throughout the U.S.
Data cited by the firm in the report clearly supports that thesis, too on various fronts, including:
-although 1 billion square-feet of the country's total warehouse inventory was built over the last ten years, it accounts for only 11% of the country's total warehouse inventory of 9.1 billion square-feet, which CBRE said its becoming increasingly obsolete at an average age of 34 years, up from a previous average of 26 years during that span;
-nearly 1 billion square-feet of total warehouse inventory is more than 50 years old and has clear heights of less than 20 feet—well below logistics tenant requirements; and
warehouses built since 2008 are generally three times larger than older ones and account for only 4% of the nation's total number of buildings
“Markets with the newest warehouses tend to have ample developable land and are near major population centers, while markets with the oldest warehouses tend to serve heavy industrial and shipping centers,” the report said. “Given the low share of modern warehouse space and the rise of e-commerce, there's ample opportunity to develop new warehouses and rebuild physically obsolete ones in the best infill locations.”
Based on CBRE data, the Northern New Jersey market has the highest weighted average age for warehouse inventory at 57. Rounding out the top five are Pittsburgh at 56, with Boston, Philadelphia, and Cleveland each with 44. And on the other end the newest markets, in terms of lowest weighted average age for warehouse inventory are the Inland Empire at 20, Las Vegas at 23, Phoenix at 26, and Salt Lake City, Nashville, Indianapolis, and Atlanta, each at 29.
In an interview, Adam Mullen, a senior managing director for CBRE's Industrial & Logistics business in the Americas, said that with newer, larger and more efficient warehouses accounting for 11% of total U.S. warehouse inventory, it is placing emphasis on more development.
“However, owners and developers remain very thoughtful and deliberate about where they invest their capital,” said Mullen. “Supply and demand remains balanced because of this measured response from developers, paired with sustained demand from users. In context, about one fourth of all of our industrial transactions are related to e-commerce. CBRE conducts an industrial transaction, on average, about every nine minutes of the business day. That demand extends to all facets of the supply chain, and better-equipped facilities are coveted by users from all industries.”
In data analysis for 56 major U.S. markets, a key finding from CBRE showed that the majority of facilities built before the mid-2000s have certain limitations that hinder e-commerce distribution usage, including low ceilings, small footprints, uneven floors, and inadequate docking.
Mullen explained that these facilities can be modernized with the caveat that the scope of that opportunity may be limited.
“For well-located facilities, roofs can be raised, dock doors can be added and parking lots can be expanded,” he said. “But the tradeoffs have to ‘pencil out' and be feasible. Location alone could potentially attract the right tenant to forego a more efficient building in exchange for a location that allows for better and faster access to the customer, which dramatically contributes to better service. For facilities located farther from population centers, the circumstances may favor redeveloping the building or seeking higher and better uses for it. Inefficient space can have major implications on the cost of running an operation. Labor is the third most expensive piece of the supply chain, after transportation and inventory-carrying costs. And an inefficient layout can impede workforce performance.”
When it comes to leveraging new development opportunities nationwide, Mullen said industry stakeholders are able to do this by by investing in the “right” speculative development and chasing available build-to-suit opportunities in major gateway markets.
“Many stakeholders have strived to tie up land and potential development sites to allow them to be in the right place at the right time,” he said.” That strategy is paying off. Institutional investors and owners have found the right balance of leveraging the opportunity and hand and of keeping occupiers' interests first. It's a strong and generally balanced marketplace.”
SC
MR
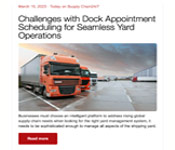
Latest Supply Chain News
- April manufacturing output slides after growing in March
- Q1 sees a solid finish with positive U.S.-bound import growth, notes S&P Global Market Intelligence
- World Trade Centers offers a helping hand to create resilient, interconnected supply chains
- 6 Questions With … Sandeep Bhide
- MIT CTL offering humanitarian logistics course
- More News
Latest Podcast
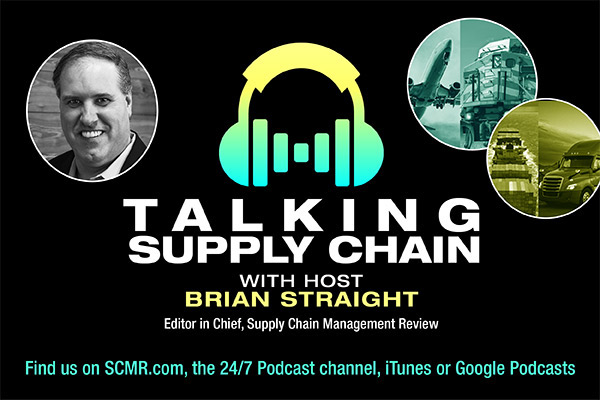
Explore
Topics
Latest Supply Chain News
- April manufacturing output slides after growing in March
- Q1 sees a solid finish with positive U.S.-bound import growth, notes S&P Global Market Intelligence
- World Trade Centers offers a helping hand to create resilient, interconnected supply chains
- 6 Questions With … Sandeep Bhide
- MIT CTL offering humanitarian logistics course
- Bridging the ESG gap in supply chain management: From ambition to action
- More latest news
Latest Resources
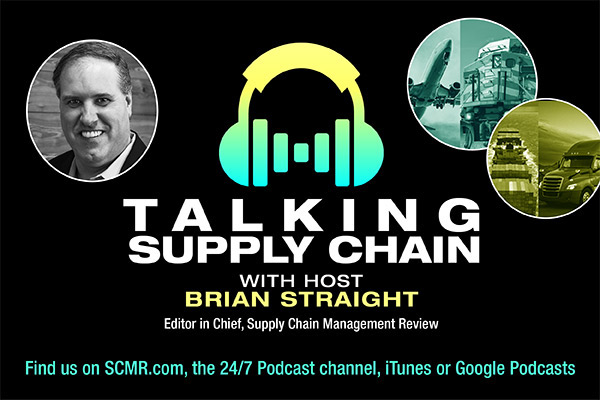
Subscribe
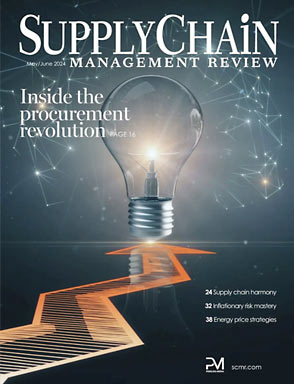
Supply Chain Management Review delivers the best industry content.
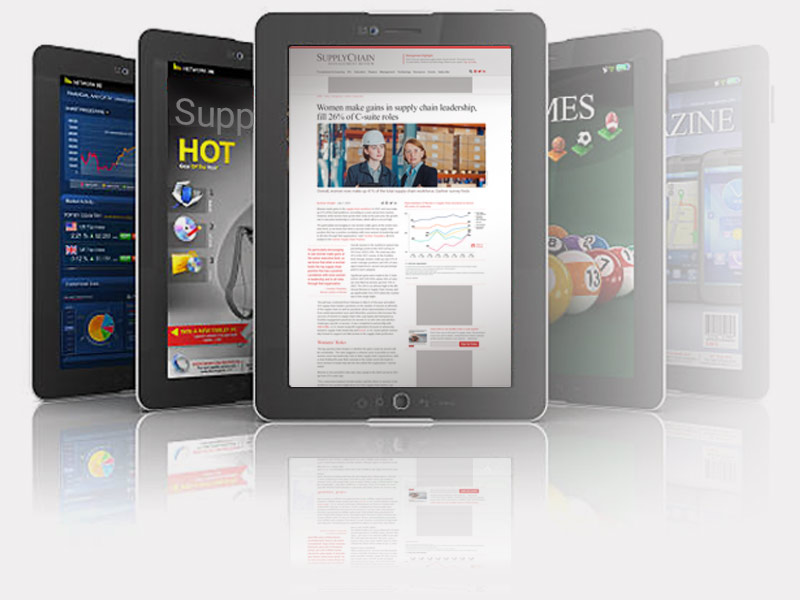
Editors’ Picks



