Editor’s Note: John Kloosterman is the co-chair of the Business and Human Rights Practice Group and a shareholder at Littler Mendelson. Michael Congiu is the co-chair of the Business and Human Rights Practice Group and a shareholder at Littler Mendelson.
It is hard to imagine an industry that more broadly impacts our personal and professional lives. The electronics and information communication technology (ICT) industry has democratized access to information and, depending on perspective, has profoundly connected or polarized our world. These sociological questions aside, we also fundamentally rely on mobile and other electronic devices to carry out our work – whether through a smartphone, tablet, or other computing device.
On a parallel track, the concepts of business and human rights continue to renovate how business views its place in the world, and its relationships to its customers, markets, and the states where it has operations. These somewhat coextensive and shifting paradigms provoke broad and complicated questions about the future of corporate citizenship and sustainability, as well as more personal and discrete questions about the role we play as consumers and how we interact with available technologies.
Unpacking these matters starts, to a point, with business assuming an awareness of and commitment to human rights issues, and gaining a better understanding as to how these devices are made and by whom. The former represents a growing consensus among companies both within and beyond the ICT industry. The latter is easier said than done. Many of our favorite devices are the product of supply chains that pass through suppliers and workers in Africa, China, Southeast Asia, California and a host of other locations before reaching our pockets and briefcases.
Exploring a particular “supply chain” must account for the reality that “supply chains” are rarely, if ever, linear or static. Supply chains contain a company's suppliers, plus the suppliers' suppliers, those second-level suppliers' suppliers, and so on, and these entities may change based on reasons that do not link back to the company selling the final product. Indeed, the processors that make our devices functional start out as minerals – gold, cassiterite (tin), tungsten and coltan (tantalum). Once extracted, the minerals may pass through the hands of several trading houses and other middlemen, before being sold to an exporter who ships the minerals to a refinery, where they are made into metal; once refined into metal, tracing the source of the minerals can be impossible. Before the refining, tracing the origin of the minerals is theoretically possible but practically impossible because of the number of traders and exporters involved.
The ICT Benchmark
One organization has sought to benchmark 20 publicly traded ICT companies using various human rights criteria that focus on forced labor. KnowTheChain.org has described this initiative as follows:
[The chosen] companies were selected on the basis of their size (market cap) and the extent to which they derive revenues from physical products as opposed to services. KnowTheChain assessed information available on each company's own website as well as additional public disclosure that over half of the companies provided in response to engagement questions.
The companies were evaluated using a methodology with seven themes: commitment and governance; traceability and risk assessment; purchasing practices; recruitment; worker voice; monitoring; and remedy.
See ICT Benchmark Finding Report, at https://knowthechain.org/wp-content/plugins/ktc-benchmark/app/public/images/benchmark_reports/KTC_ICT_Benchmark_Findings_June.pdf.
This Benchmark's 2016 findings reflect the realities of the changing business and human rights landscape and the profound challenges in effective supply chain management. For example, the Benchmark's findings reflect that “[e]ighteen of the 20 companies benchmarked have publicly demonstrated awareness of and commitment to addressing forced labor in the supply chain. However, far fewer of these companies also have strong processes in place to implement these commitments.”
While most of the benchmarked companies—and a growing number of companies within and beyond the ICT industry—have public human rights commitments, effectively implementing these commitments amongst an often interdependent and fluid set of organizations within a supply “chain” presents great challenges.
A Way Forward?
In this complex space, the first steps can be the most difficult, and our thoughts on a way forward focus on (1) how to make a public commitment to these issues; and (2) how to implement that commitment. This exercise can and should be dynamic and fluid, and necessarily based on the specific risks in a company's particular operations and industry. The UN Guiding Principles were flexibly designed to allow for companies to flexibly implement their own operationally-specific commitments. With that in mind:
1. Public commitments about your human rights practices, whether found in a code of conduct or supplier code of conduct, should avoid general pronouncements that cannot be reasonably or practically followed. Similarly, simply adopting ILO standards or agreeing to follow voluntary international standards (like the UN Global Compact) should not occur without understanding attendant consequences. Company and supplier codes of conduct should be viewed as legal documents that reflect promises that the company actually expects to keep. While aspirational statements and commitments are well-intentioned and can be laudable, the wiser course is to partner with legal counsel and stakeholders to develop commitments to specific human rights risks that are particularly prominent to the company and its industry and that the company can practically and positively impact.
2. Look to existing laws for implementation templates. For example, the California Supply Chains Act can serve as an implemental roadmap. The Supply Chains Act, similar to the UK Modern Slavery Act and legislation pending in the EU, requires covered companies to report on five areas: (i) third-party verification of supply chains to evaluate the risk of forced labor and trafficking; (ii) conducting independent, unannounced audits of suppliers; (iii) requiring suppliers to certify that materials incorporated into the product comply with local laws on forced labor and human trafficking; (iv) maintaining internal accountability standards and procedures for employees and contractors regarding trafficking and forced labor; and (v) providing training on trafficking and forced labor issues to employees with responsibility for supply chain management.
This California law does not require action in these identified areas. It simply requires that a company report what it is, or is not, doing in these identified areas. That said, companies that take action in these five areas will better position themselves to develop intelligent policies and be better positioned to implement those policies and, to a degree, better position the company in the future of the ICT industry and broader market.
SC
MR

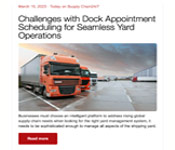
Latest Supply Chain News
- Few executives believe their supply chains can respond quickly to disruptions
- Technology’s role in mending supply chain fragility after recent disruptions
- Tech investments bring revenue increases, survey finds
- Survey reveals strategies for addressing supply chain, logistics labor shortages
- Israel, Ukraine aid package to increase pressure on aerospace and defense supply chains
- More News
Latest Podcast
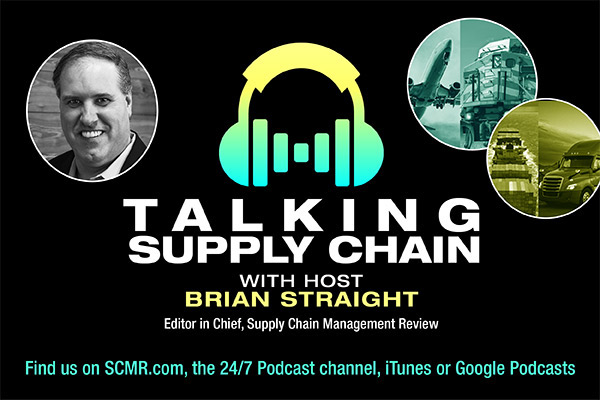
Explore
Topics
Latest Supply Chain News
- Few executives believe their supply chains can respond quickly to disruptions
- Technology’s role in mending supply chain fragility after recent disruptions
- Tech investments bring revenue increases, survey finds
- Survey reveals strategies for addressing supply chain, logistics labor shortages
- Israel, Ukraine aid package to increase pressure on aerospace and defense supply chains
- How CPG brands can deliver on supplier diversity promises
- More latest news
Latest Resources
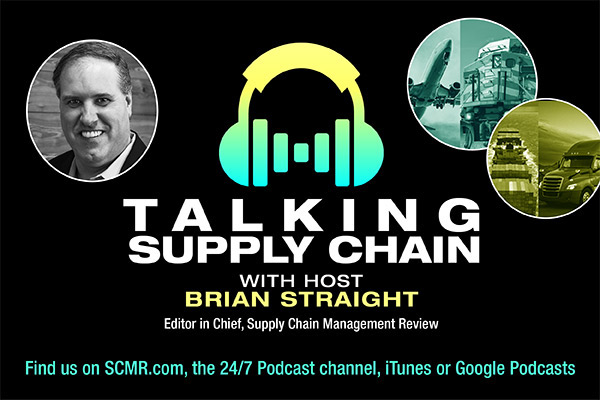
Subscribe
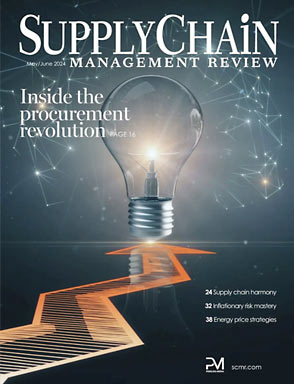
Supply Chain Management Review delivers the best industry content.
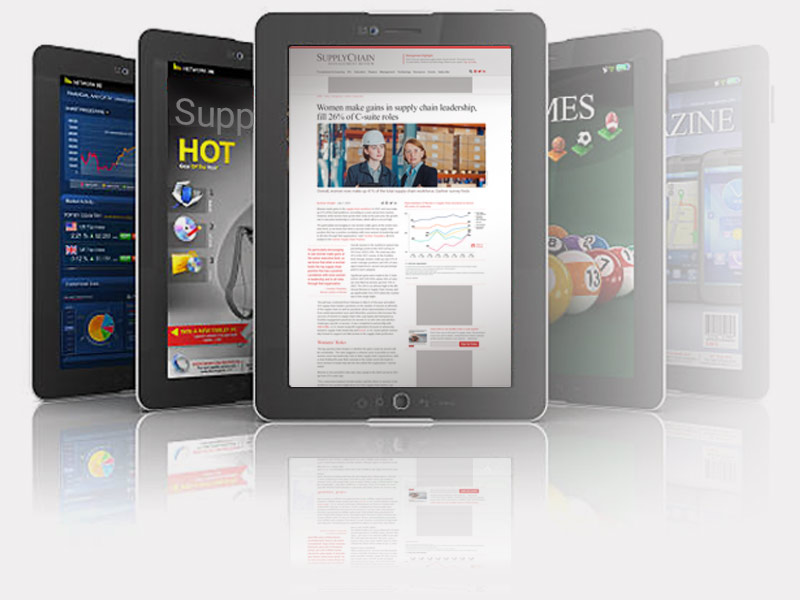
Editors’ Picks



