If you are a small almond processor and suddenly global superstar Taylor Swift was seen eating your almonds with boyfriend Travis Kelce, would that be good for your business?
It could be. It could also sink the business as demand soars but you are unable to meet the product demand, creating ill will toward your brand and causing customers to turn to other options. That is the world in which sales and operations planners (S&OP) live. Demand suddenly rises, so how do you satisfy it without building up too much inventory once that demand subsides and perhaps bankrupting the company?
“We exist for one reason, for a customer, right?” Kira Bilecky, senior supply chain consultant at St. Onge Company, asked her audience at the recent Modex 2024 conference in Atlanta. “We call that our demand side. We have to meet customer expectations. Now, in today’s world, unfortunately, customers want every product or every flavor, every packaging size—a six-ounce can, a 25-ounce bag, 1.5-ounce sleeves, habanero, barbecue, salt and vinegar, a variety of flavors. So it’s constantly changing and we as a business need to be able to serve those demand lead times.”
Planning for demand spikes
Bilecky walked attendees through the S&OP process using almonds as her product and showing how planners can better be prepared for that business spike the Taylor Swift exclusive photo will create.
The almond example is specific in that it is tied to a seasonal product, but Bilecky said that all planners must address these types of issues to balance demand. Taylor Swift eating your almonds may be great, but it may mean making some tradeoffs.
“We exist for one reason, for a customer, right?. We call that our demand side. We have to meet customer expectations. Now, in today’s world, unfortunately, customers want every product or every flavor, every packaging size—a six-ounce can, a 25-ounce bag, 1.5-ounce sleeves, habanero, barbecue, salt and vinegar, a variety of flavors. So it’s constantly changing and we as a business need to be able to serve those demand lead times.”
Aligning supply demand with financials and how it all fits into the overall business strategy is critical, Bilecky said. “Every functional area participates in this process,” she added, noting that S&OP “facilitates a lot of uncomfortable decisions.”
Whether to satisfy that Taylor Swift demand for your almonds will ultimately come down to your other customers, Bilecky said. Will meeting this unusual, likely one-time demand blip jeopardize existing relationships? The decision may be made to miss the sudden spike.
“At some point you have to be okay saying no. And again, S&OP helps to make those decisions,” Bilecky said.
Bilecky laid out a five-step process to ensure your S&OP process is set up to make these types of hard decisions. They are:
- Aggregate data. Collect all the data that will impact planning, including sales data, financial data and product lifecycle management data.
- Marketing. What is the marketing department planning? Are there any promotions that impact demand? Build a demand forecast at this point.
- Identify supply and demand risks. Is there anything that could alter demand for your product? Could there be a raw material shortage? Are your suppliers secure?
- Identify any gaps. Will supply meet demand (too much or too little)? Is there too much or too little inventory?
- Tie it all together. This includes financials and the enterprise-wide impact
“Sometimes it may come down to a critical decision that needs to be escalated to the highest level, and [step 5] is the place that it happens,” Bilecky said. “Ultimately, you walk out of your monthly cycle with one cohesive plan that the entire company gets behind.”
Stumbling blocks
That last point is where many organizations stumble. Looking back to her professional soccer playing career, Bilecky explained why teamwork really matters in this process.
“I used to play defense. We get credit for nothing and I’m okay with that, or at least I came to terms with it,” she said. “And one of my goals for the game would be, I don’t want my goalie to touch the ball the whole game because that means we have a better chance of winning or at least not losing. However, my goalie really likes to have a lot of saves in games. So right there you can see we’re in direct conflict with one another on how we perceive my individual goal versus their goal versus the team’s goal. So again, this is about aligning and getting everybody to play on the same team and achieve that goal.”
Bilecky went on to detail many of the steps in the process, but ultimately, a successful S&OP strategy will come down to good data, better forecasting, and execution. All of this should be done on a monthly basis at a minimum, which allows an organization to respond quicker to deviations.
“So the benefits of S&OP and inventory management, of removing functional silos, of addressing all your functional concerns … is you can all have that conversation around what’s important, improving coordination, communication, teamwork,” she said. “I do think getting everybody in the room on the same page is really powerful and allows people to really see [impacts].”
SC
MR

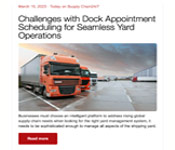
More Sales & Operations Planning
What's Related in Sales & Operations Planning

Explore
Topics
Procurement & Sourcing News
- April manufacturing output slides after growing in March
- World Trade Centers offers a helping hand to create resilient, interconnected supply chains
- Bridging the ESG gap in supply chain management: From ambition to action
- Israel, Ukraine aid package to increase pressure on aerospace and defense supply chains
- How CPG brands can deliver on supplier diversity promises
- How S&OP provides the answer to in-demand products
- More Procurement & Sourcing
Latest Procurement & Sourcing Resources
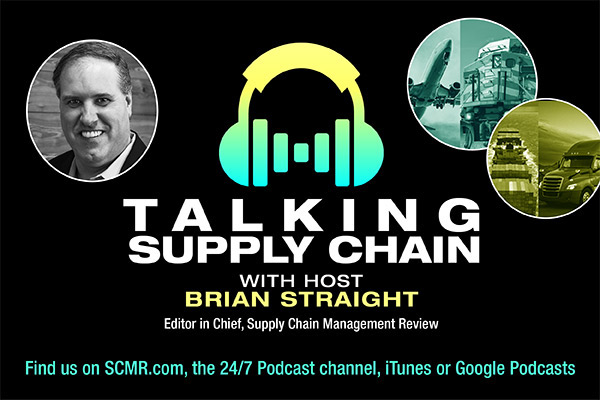
Subscribe
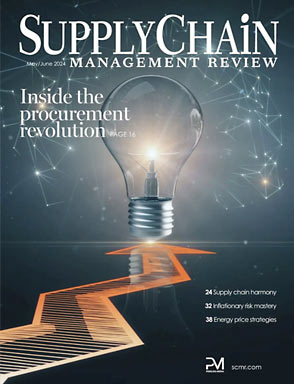
Supply Chain Management Review delivers the best industry content.
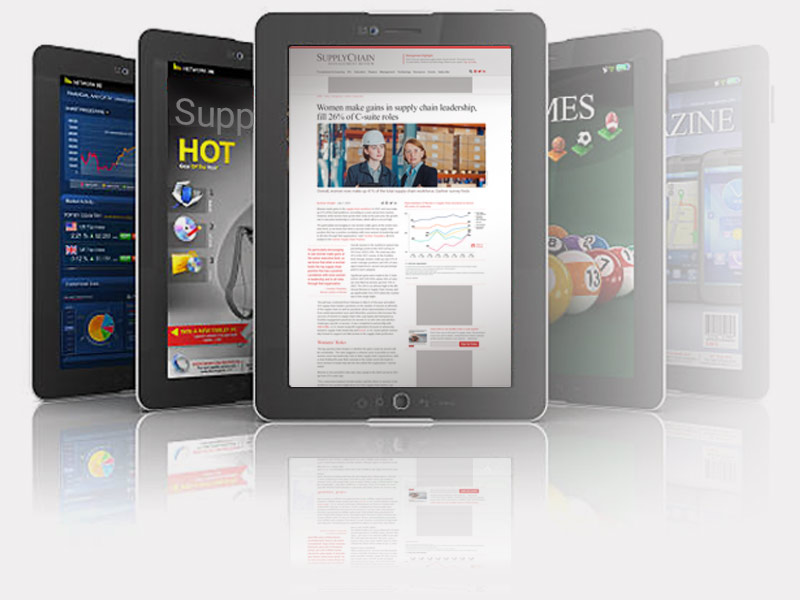
Editors’ Picks



