Sorry, but your login has failed. Please recheck your login information and resubmit. If your subscription has expired, renew here.
May-June 2016
The procurement function is at an inflection point.” So begins “The reinvention of procurement," an article by Jonathan Hughes and Danny Ertel, partners at the Boston-based consulting firm Vantage Partners. The authors argue that while many leading companies have transformed their procurement organizations into a linchpin of their enterprise strategy, far too many others remain trapped by procurement models that are out of date in today’s fastpaced economy, where the acquisition of innovation, collaboration, services and solutions is more important than transactions based on the lowest cost per unit. Reinvention is a fitting theme for… Browse this issue archive.Need Help? Contact customer service 847-559-7581 More options
To promote efficiency and effectiveness, organizations are encouraging collaboration among related functions within the enterprise. Two areas for which this makes sense is the research and development (R&D) or product engineering group and the procurement group. In product development, members of the procurement group can provide insight regarding the purchasing of product components. Some organizations are going a step further to involve select external partners as well. In fact, APQC’s Open Standards Benchmarking data in product development indicates that 66% of organizations involve their suppliers in new product or service development, including product improvements and extensions. In turn, members of the R&D function can be involved in the selection of suppliers to ensure the best supply of components and materials.
APQC’s research indicates that organizations encouraging collaboration between the R&D function and suppliers can take advantage of benefits such as a reduction in the total cost to manufacture a product or easier sourcing of components. Involvement of the R&D function in supplier selection and appraisal can lead to lower procurement costs. However, these benefits may come at the expense of some aspects of procurement efficiency.
Supplier involvement in product development
The amount that organizations involve their suppliers in the product development process varies, with only about 31% of organizations having extensive participation of suppliers in these efforts. Those that do have extensive participation can create opportunities that are mutually beneficial. APQC has found that one way organizations accomplish this is by involving suppliers in the management of cost targets for new products and their components. Organizations communicate cost targets for products or components to their suppliers at varying stages of the development process. As shown in Figure 1, a similar number of organizations communicate cost targets to suppliers during the design stage of product development as during the sourcing stage. Only about 19% of organizations communicate targets to suppliers during the earlier stages when product specifications and concept designs are developed, and about one-third of organizations do not communicate cost targets to their suppliers at all.
![]() |
This complete article is available to subscribers
only. Click on Log In Now at the top of this article for full access. Or, Start your PLUS+ subscription for instant access. |
SC
MR
Sorry, but your login has failed. Please recheck your login information and resubmit. If your subscription has expired, renew here.
May-June 2016
The procurement function is at an inflection point.” So begins “The reinvention of procurement," an article by Jonathan Hughes and Danny Ertel, partners at the Boston-based consulting firm Vantage Partners.… Browse this issue archive. Access your online digital edition. Download a PDF file of the May-June 2016 issue.![]() |
Download Article PDF |
To promote efficiency and effectiveness, organizations are encouraging collaboration among related functions within the enterprise. Two areas for which this makes sense is the research and development (R&D) or product engineering group and the procurement group. In product development, members of the procurement group can provide insight regarding the purchasing of product components. Some organizations are going a step further to involve select external partners as well. In fact, APQC's Open Standards Benchmarking data in product development indicates that 66% of organizations involve their suppliers in new product or service development, including product improvements and extensions. In turn, members of the R&D function can be involved in the selection of suppliers to ensure the best supply of components and materials.
APQC's research indicates that organizations encouraging collaboration between the R&D function and suppliers can take advantage of benefits such as a reduction in the total cost to manufacture a product or easier sourcing of components. Involvement of the R&D function in supplier selection and appraisal can lead to lower procurement costs. However, these benefits may come at the expense of some aspects of procurement efficiency.
Supplier involvement in product development
The amount that organizations involve their suppliers in the product development process varies, with only about 31% of organizations having extensive participation of suppliers in these efforts. Those that do have extensive participation can create opportunities that are mutually beneficial. APQC has found that one way organizations accomplish this is by involving suppliers in the management of cost targets for new products and their components. Organizations communicate cost targets for products or components to their suppliers at varying stages of the development process. As shown in Figure 1, a similar number of organizations communicate cost targets to suppliers during the design stage of product development as during the sourcing stage. Only about 19% of organizations communicate targets to suppliers during the earlier stages when product specifications and concept designs are developed, and about one-third of organizations do not communicate cost targets to their suppliers at all.
![]() |
SUBSCRIBERS: Click here to download PDF of the full article. |
SC
MR
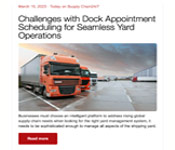
Latest Supply Chain News
- Few executives believe their supply chains can respond quickly to disruptions
- Technology’s role in mending supply chain fragility after recent disruptions
- Tech investments bring revenue increases, survey finds
- Survey reveals strategies for addressing supply chain, logistics labor shortages
- Israel, Ukraine aid package to increase pressure on aerospace and defense supply chains
- More News
Latest Podcast
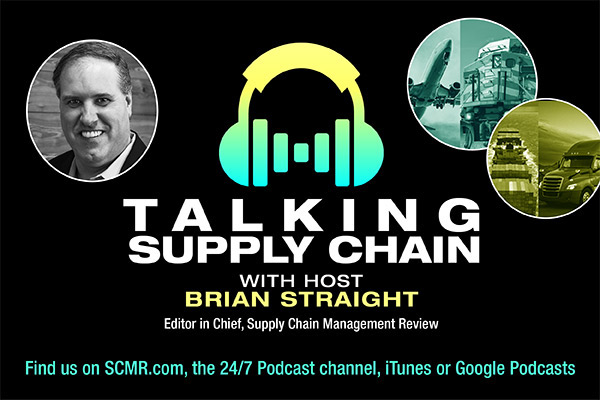
Explore
Procurement & Sourcing News
- Israel, Ukraine aid package to increase pressure on aerospace and defense supply chains
- How CPG brands can deliver on supplier diversity promises
- How S&OP provides the answer to in-demand products
- There is still work to do to achieve supply chain stability
- Blooming success: The vital role of S&OE in nurturing global supply chains
- How one small part held up shipments of thousands of autos
- More Procurement & Sourcing
Latest Procurement & Sourcing Resources
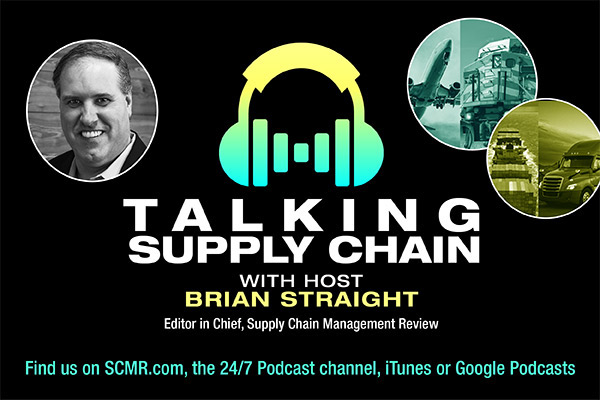
Subscribe
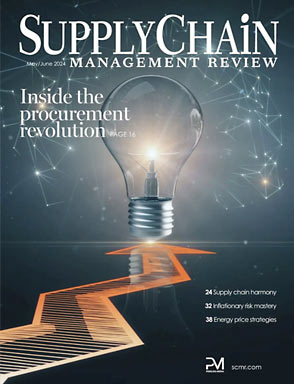
Supply Chain Management Review delivers the best industry content.
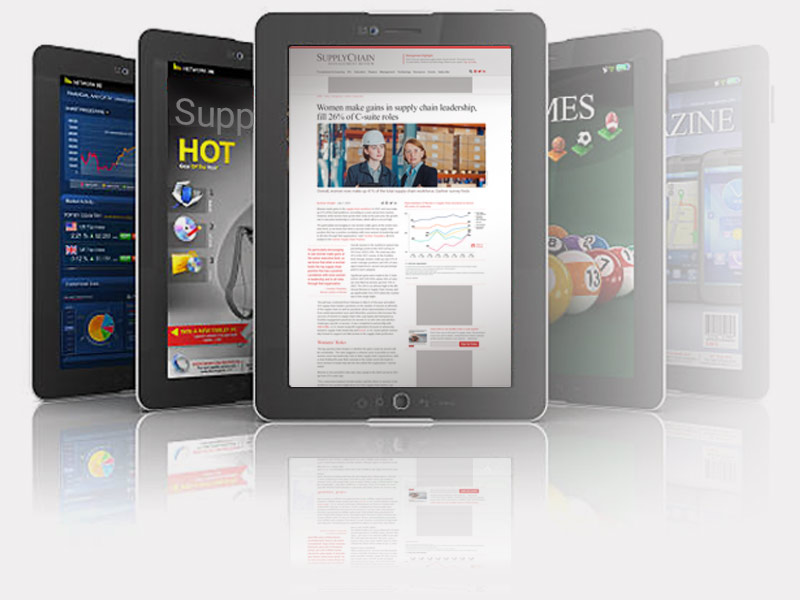
Editors’ Picks



