The distance and volume of food shipped has skyrocketed during the last few decades, but according to Forbes Magazine, so has the amount of food spoilage, approximately $35 billion per year. Global fish loss due to spoilage is estimated at 10-12 million tons per year; estimates have indicated that up to 1/3 of all produce is sold at a steep discount because of expiration; and an estimated 80,000 pigs die each year due to stressful and injurious transit. What’s more, some studies have found that a potential bioterrorist “infection” at a single point in US cattle production could result in a loss of 23 million cattle within eight days of attack.
Regardless of how far up or downstream the supply chain you look, the risk to the food supply chain is significant. Since the quality of logistics design and execution within food transport significantly contributes to overall food spoilage, safety, and quality, the entire supply chain must have hardened logistics structures designed and in place which enable security and traceability. Added logistics scrutiny and monitoring is imperative – inadequate logistics operations not only lead to product loss, but also have the ability to add to product contamination, potentially spreading diseases to other animals or humans.
Injection of relevant technology enablers, increased partner collaboration, and the adoption of rigid processes can minimize this risk. Ensuring constant visibility into freshness at any certain point will help determine shelf life, thereby reducing spoilage, and improving delivered freshness and quality.
Staying competitive is a business reality, but minimizing losses is vital. Are you spending your risk management time, money, and effort in the best areas for your business needs?
Challenges & Solutions
Numerous operational challenges build up to contribute significant enterprise risk to the overall food supply chain, including longer distances between harvest/processing/consumption points to lack of enterprise-wide partnership collaboration and real-time visibility of product freshness.
Thorough due diligence and background checks can help eliminate unsuitable prospective service providers. Strong partnerships among logistics providers can be developed and maintained through stringent communication and collaboration procedures. It is particularly important to have strong relationships between the shipper and transporter to provide a platform to execute on common goals and objectives. Identification of expectations need to be established early in the process ,and the use of logistics control towers can be used to help maintain constant visibility and provide real-time decision making to potentially divert product to differing markets depending on freshness. Lastly, develop and monitor appropriate, success-driven and behavior-driving metrics and Key Performance Indicators (KPIs) to ensure your strategy is a success.
Every food product’s operating environment is unique and tailoring will most certainly be required, but the following common considerations should be integrated into your supply chain to ensure successful and safe movement from origin to destination.
Identify Component Logistics Partners
There are a multitude of capable service providers in the market with differing operational structures. Of course, having your own internal or private fleet is easiest to control, but you need to evaluate total cost of ownership, branding benefits and other variables to ensure it’s a good fit. If an external service provider (e.g., transporter) is necessary, an in depth evaluation must be performed to ensure the transporters offer the capability you desire, and are also experienced, safe, and trustworthy.
Review their Track Record
Regardless of who’s doing the transport, it’s encouraged to perform thorough research into the marketplace and do your homework. Evaluate partner backgrounds, reputations, and most importantly, capabilities. Ask for references, and when you ask, ensure that the transporters have your goals and objectives in focus; ensuring partner credibility is key, so perform reference checks to ensure that their service is exemplary.
Define your expectations clearly, and explain “what success looks like”
Ensure both parties have clear expectations from the beginning. It is essential to build a true partnership with both parties working toward the same goal. Promote a “vested” relationship concept from the beginning where both teams are working toward common goals. Ensure that a contract or memorandum of agreement is created to avoid confusion and prevent disagreement and litigation.
Monitor this continued partnership success with logistics control towers
Monitor the operation and continued successes using logistics control towers, which are cross-divisional arrangements that make use of system-integrated information hubs to provide key insights into your supply chain process. Such towers enable a collaborative environment in which both parties will be acutely aware of operational field execution, and this will help drive success. For example, if for some reason a given shipment will not be able to be delivered prior to its expiration, both parties will be able to collaboratively make decisions to potentially divert to more localized markets to ensure that the product can be delivered safely and within freshness standards. Effectively operating control towers, in conjunction with innovative technology and transporter implants at shipper locations, can help drive freshness from place of harvest to place of consumption.
Elevate collaboration and refine the service level agreement jointly to get the job done
Take your collaboration to the next level by ensuring frequent spot checks, audits, and performance reviews. Checks and balances are necessary to keep all parties in line. Consistently evaluating processes, drivers, and equipment will ensure operational performance remains paramount. Frequently reviewing service level agreements can help to ensure both entities are not degrading performance (or causing excess cost) for the other (e.g., excessive dwell/load times at dock causing carrier delays)
Measure results that matter
Identify metrics and KPIs that will drive business behavior to obtain preset goals and objectives. Ensure these are attainable, communicated early on, and are monitored vigilantly on a daily basis. Develop contingency plans to address ineffective performance, and if results start to slip, immediately intervene with action plans to mitigate. It is recommended to maintain a log of lessons learned to potentially avoid similar troubles in the future. Contemplating performance-based payment is a good idea although quite complex.
Risk to the food supply chain is real, and with all of the added volume and distance being traveled, this risk is continuing to rise on a daily basis. Shippers must be vigilant in identifying and reviewing service providers, defining expectations, and lastly and most importantly, monitoring performance. Current technology needs to be applied to the overall strategy to help the shipper/transporter vested “team” make improved real-time decisions in the event of infrastructure, environmental, or freshness issues.
A focus on upfront planning, monitoring, and evaluation will help businesses save significant amounts of money over time. Transporting food will always have risk, but lowering risk equates to reduced costs. How much avoidable cost is your company hemorrhaging by not focusing on risk in the food supply chain?
SC
MR
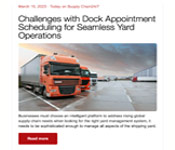
Latest Supply Chain News
- Despite American political environment, global geopolitical risks may be easing
- Joseph Esteves named CEO of SGS Maine Pointe
- Employees, employers hold divergent views on upskilling the workforce
- April manufacturing output slides after growing in March
- Q1 sees a solid finish with positive U.S.-bound import growth, notes S&P Global Market Intelligence
- More News
Latest Podcast

Explore
Latest Supply Chain News
- Despite American political environment, global geopolitical risks may be easing
- Joseph Esteves named CEO of SGS Maine Pointe
- Employees, employers hold divergent views on upskilling the workforce
- April manufacturing output slides after growing in March
- Q1 sees a solid finish with positive U.S.-bound import growth, notes S&P Global Market Intelligence
- World Trade Centers offers a helping hand to create resilient, interconnected supply chains
- More latest news
Latest Resources

Subscribe
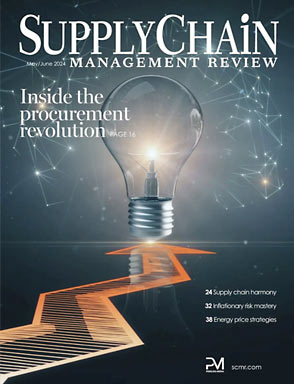
Supply Chain Management Review delivers the best industry content.
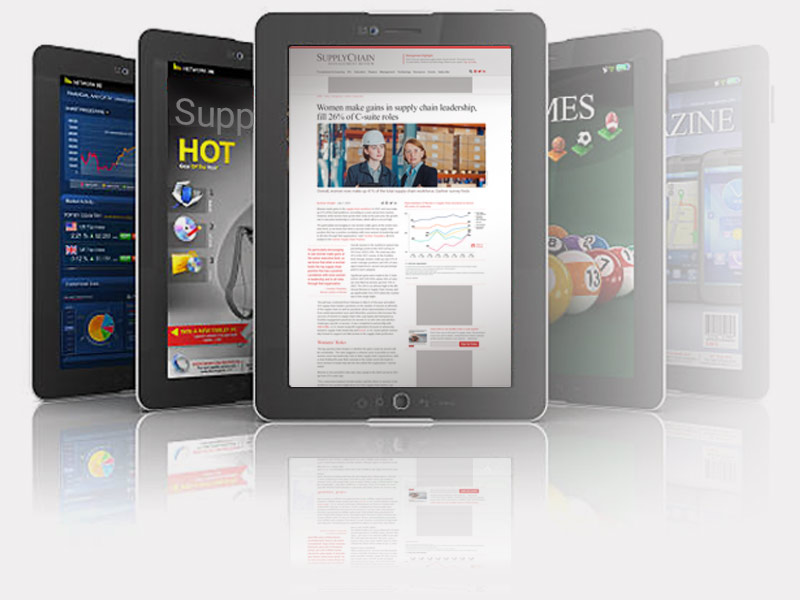
Editors’ Picks



