This morning, I taught my first full class in front of a computer instead of in front of my students. Like nearly all universities, Penn State has cancelled in-person classes and is moving to remote/online instruction. My class is for seniors majoring in Supply Chain Management, and it is (and will be) somewhat awkward to teach a case-based discussion course online.
Per the syllabus, the already scheduled topic of supply chain risk management is taking on a whole new urgency for many firms, industries and society as a whole with the spread of COVID-19. It seemed like a good time to share some of what we are and will be talking about in class with our supply chain partners.
A caveat: My research expertise is in supply chain decision-making; with Christopher Craighead, now at the University of Tennessee and an SCMR contributor, I co-wrote a popular case about how firms can deal with a supply chain disruption. Yet, that was a bankruptcy of a supplier and the impact on a Tier-1 firm. Today the news is about Disruption with a capital “D”. So, what are some differences between COVID-19 and other disruptions? There could be more, yet I discuss seven dimensions in this article, which are summarized in Table 1:
Geography: In most cases, a supply chain disruption is limited to a region or country. For example, we are used to hurricanes hitting Florida, or earthquakes in California. This past year, we saw massive wildfires in Australia. No one should discount the suffering after natural disasters like Hurricane Katrina on New Orleans and other areas. Yet one difference about a pandemic like COVID-19 is that it is hitting the entire world.
This is important, because under normal circumstances, resources from one region can regularly support effected regions. For example, utilities send repair crews in from out of state, and even firefighters and equipment from the USA recently assisted in Australia. This sort of thing is difficult to do when everyone simultaneously impacted.
Scope: Beyond geography, COVID-19 has nearly unprecedented scope. In an ordinary disruption, we might see a few key industries knocked offline for weeks or months: Hurricane Harvey took much of the US Gulf Coast petrochemical industry offline for several weeks, yet West Coast refineries were not impacted. What is unique about COVID-19 is that it is impacting both goods and services. Clearly there is increased demand for masks and hand sanitizer, so it is somewhat understandable those items would be in short supply. However, there is fundamentally no increase in demand for toilet paper, so shortages there are unusual and related to human behavior. Instead, the impact of COVID-19 is that demand for services is greatly diminished. We cannot stockpile inventory of services or experience goods, so those are at best delayed. This includes things like all sporting events cancelled, all cruise ships idled, unused hotel rooms and widespread cancellations of airline flights. In addition, many shops and restaurants are also closing. Last week, I went into my local barber shop (as yet we had no COVID-19 cases reported in my county or nearby). There were six employees standing outside; I was the only customer in the shop the whole time. Here in State College, much of the economy revolves around university students, who are now staying home. All of this will have knock-on effects throughout the entire economy.
Demand vs. Supply: Many supply chain disruptions impact supply. I have already mentioned several, and today in class the previously assigned reading was about a well-known fire in a Philips Electronics chip plant in 2001 the impact on major mobile phone makers Nokia and Ericsson. At the time, Nokia had 27% of the global cell phone market, and Ericsson had 12%. Lightning struck the Philips plant, causing a loss of chips, yet the real damage was that the plant was contaminated and could no longer produce chips for these and other firms. However, what was unique was how Nokia responded, with fast communication, an all-hands on deck approach and coordination that saw them weather the storm with minimal disruption. Ericsson took a much slower approach and was far more vulnerable to this supply disruption. In the end, Nokia gained 3% of the global cell phone market (mostly from Ericsson), and subsequently Ericsson ended up exiting the handset business. There have been some supply disruptions due to COVID-19, and there will be more disruptions in manufacturing, distribution and transportation in the upcoming weeks.
However, COVID-19 is (and will be) impacting demand. Perhaps you have seen news reports about major airlines cancelling all international flights, and 40% of their domestic capacity. Beyond this, demand will be impacted even when there is virtually no disruption in supply. For example, look to the Fukushima Daiichi nuclear disaster following the earthquake and tsunami in Japan in 2011. Shortly after the disaster, luxury goods maker LVMH closed 50 stores in Japan. The supply chain for high end merchandise was relatively unaffected, yet few people wanted to be seen with a new Louis Vuitton handbag when tens of thousands of their neighbors were suffering. Other luxury brands were similarly affected.
In the case of COVID-19, it remains to be seen what the impact will be. For example, one can easily imagine that the demand for new cars will decrease, both because some individuals may lose their jobs or see hours cut and understandably reduce their spending. Yet demand will also decrease because the perception of conspicuous consumption of new goods is likely to muted demand in the face of a global disaster.
Prior Planning & Experience: For many disruptions, planning and prior experience are guides. For example, factories in the Midwest and elsewhere have tornado-safe locations for their employees.
Elementary schools regularly practice fire and tornado drills. Refineries in the gulf coast plan for hurricanes, and hospitals have emergency generators. Yet there is limited prior planning for a global pandemic such as COVID-19. Yes, the USA has a strategic stockpile of ventilators and other supplies, yet no amount of inventory would be sufficient under the worst-case scenarios.
Perhaps more important than inventory and planning is the lack of experience: Experts refer back to the 1918 Spanish Flu outbreak for guidance, yet no public health experts have personal experience with this type of global pandemic. (The contrast between Philadelphia and St. Louis is telling, as the former went ahead with a large, public parade with after which thousands of additional individuals became infected with influenza; St. Louis experienced far fewer cases and deaths after implementing quarantine procedures.) It is good that we do not regularly have pandemic events, yet these are unprecedented times for firms, individuals and world leaders who may not know the best steps to take.
Financial System: Most of the time, when there is major disruption, the financial impact is relatively contained. Events such as Pearl Harbor and 9/11 saw a comparably small impact to the stock market. The closest thing might be the global financial crisis in 2007-08. Yet that financial crisis had a comparatively a limited supply chain impact. If anything, there was more supply and less demand, yet after air travel was restored, there was no major, sustained disruptions to production or transportation networks. In contrast, we have seen global stock markets crash, and central banks undertake unprecedented actions to support the economy. The reason for this is that the COVID-19 demand shock is leading to a financial disruption. If this continues, we will see small businesses cut employees or close and many firms will have difficulty raising capital or repaying loans; preserving cash will be crucial.
Term: For most disruptions, the term is limited, or at least is quantifiable. For example, most disasters see short-term demand for rescues or emergency services immediately after an event. However, the term for COVID-19 is relatively unknown. The demand for hospital beds and ventilators is likely to increase, and the social distancing that is being implemented is designed to delay the time of peak infections and keep it below the system capacity. Yet the larger point is that most large disruptions have a defined term that can be predicted, and the term for a global pandemic is longer and uncertain.
Human Impact & Behavior: For most disruptions, the human impact is relatively limited. Naturally, there are immediate and consequential injuries following a natural disaster. Yet these are limited by location and are somewhat understandable: Natural disasters can be terrifying, yet fear largely subsides when they are over. In contrast, COVID-19 has many unknowns. Most of us are not yet infected, yet it is natural to be concerned for family members and friends. We do not know how long this will last, nor what the consequences will be. I doubt that many of us would prefer to live through a major tornado rather than practice social distancing, yet we should not discount the impact on behavior. That is perhaps one reason that stores are running short of toilet paper: People feel the need to do something to prepare, even if the underlying consumption of toilet paper remains constant.
Other Impacts: Naturally, there could be other effects. For example, many pharmaceuticals and machine parts are made in Switzerland, and these are regularly shipped worldwide in the cargo space of commercial airliners. If the global air network is disrupted over the long term, this could lead to shortages or other impacts. In addition, firms and governments are likely to re-consider their supply chains to reduce systemic risk. There will be considerable work to re-design supply chains for to improve resiliency. Much of the global pharmaceutical industry relies on materials made in China, and many industries (like automotive) have complex supply chains. The point here is that all of these relationships will need to be reexamined.
What to Do: Clearly, supply chain leaders should prepare for additional disruptions in supply and transportation. Yet if you are a business chain leader, what are some things you could do right now? There are some fine resources on supply chain risk management , yet most resources focus on developing a resilient supply chain and have less to do with facing an immediate crisis. As I told my students this morning, these are unprecedented times, yet we will get through these by working together and with flexibility. This is unlikely to be the last supply chain disruption, though it is likely to be one of the most memorable. Each of us should listen to public health authorities and do what we can considering the unique circumstances.
Beyond that, consider three additional steps:
First and foremost, take care of your people, including employees and customers. Employees likely will need to be re-assured about what is happening at your firm, so maintain effective communication. If anything, over-communicate, especially if there are significant changes to regular operations. Provide opportunities for employees to talk with you or their manager. For example, if employees are working from home, have their supervisor call just to check on how that is going is an easy win.
Second, be flexible, and encourage flexibility. There will be inevitable disruptions as schools remain closed, and more individuals contract or care for those with COVID-19. Letting people know they should remain home if they feel ill or are in contact with someone who has the virus is key.
Third, this is a good time to review and update emergency plans and contact information. Make sure several layers of backup employees are available for key activities, and update emergency contact lists so that these backup employees can communicate with others. Finally, months or years from now, employees and customers are unlikely to have remembered what you said, yet they are likely to remember how they felt.
Brent Moritz is an Associate Professor of Supply Chain Management at the Smeal College of Business, Pennsylvania State University and a faculty affiliate of the Center for Supply Chain Research at Penn State. He holds a Ph.D. from the University of Minnesota. Prior to his academic career, Moritz held positions in manufacturing and supply chain management at BorgWarner, Eaton and Parker Hannifin. He can be reached at [email protected]. An earlier version of this article was available via the Penn State Center for Supply Chain Research and LinkedIn.
For more information, see: Latour. 2001. Trial by Fire: A Blaze in Albuquerque Sets Off Major Crisis for Cell-Phone Giants. The Wall Street Journal; New York, N.Y.; Jan. 29, 2001, p. A1
For further information, see Helper, Gray and Osborne. 2020. Retooling US Supply Chains to Address Weaknesses Exposed by new Coronavirus. Washington Center for Equitable Growth.Retrieved March 16, 2020.
Some recommended additional resources include the following:
Melnyk, Closs, Griffis, Zobel and Macdonald. 2014. Understanding supply chain resilience. Supply Chain Management Review. Jan/Feb 2014.
Chopra and Sodhi. 2004. Managing Risk to Avoid Supply Chain Breakdown. MIT Sloan Management Review, Fall 2004, pp. 53-61.
Sheffi, Y. 2005. The resilient enterprise: overcoming vulnerability for competitive advantage. MIT Press Books.
SC
MR

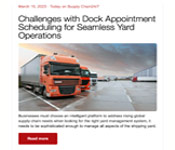
Latest Supply Chain News
- Despite American political environment, global geopolitical risks may be easing
- Joseph Esteves named CEO of SGS Maine Pointe
- Employees, employers hold divergent views on upskilling the workforce
- April manufacturing output slides after growing in March
- Q1 sees a solid finish with positive U.S.-bound import growth, notes S&P Global Market Intelligence
- More News
Latest Podcast

Explore
Latest Supply Chain News
- Despite American political environment, global geopolitical risks may be easing
- Joseph Esteves named CEO of SGS Maine Pointe
- Employees, employers hold divergent views on upskilling the workforce
- April manufacturing output slides after growing in March
- Q1 sees a solid finish with positive U.S.-bound import growth, notes S&P Global Market Intelligence
- World Trade Centers offers a helping hand to create resilient, interconnected supply chains
- More latest news
Latest Resources

Subscribe
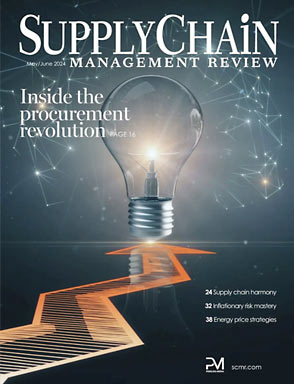
Supply Chain Management Review delivers the best industry content.
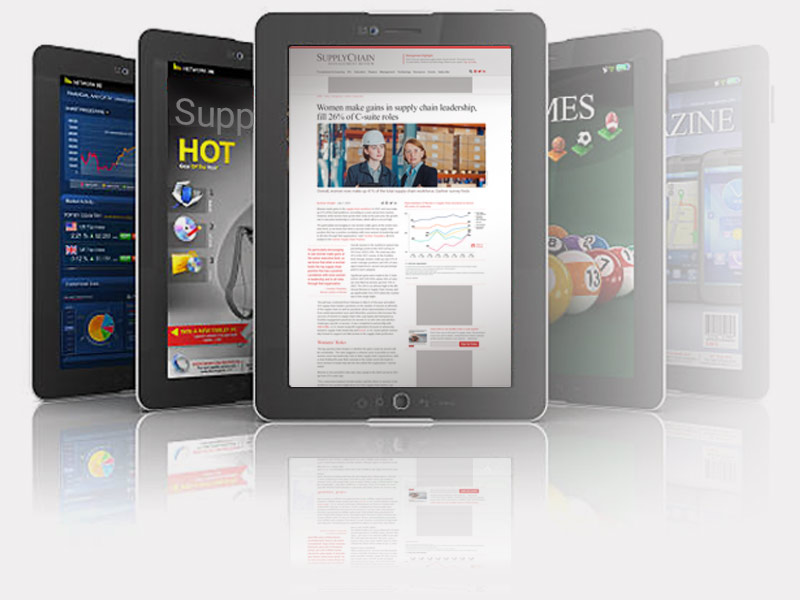
Editors’ Picks



