An increase in e-commerce sales of up to 27.6% in the last year is causing transportation and logistics (T&L) companies tremendous strain as they work to fulfill a surge in orders due to the global pandemic.
To scale their businesses and deal with changing consumer and business behaviors, a new global research report by mobile and IoT management solutions provider, SOTI, found that 74% of T&L companies had already begun to invest in mobile technology, wearables and IoT solutions in 2020. A significant 80% plan to continue to invest in mobile technology throughout 2021.
The Mobilizing the Delivery Workforce: State of Mobility in T&L 2021 Report interviewed 550 IT decision-makers in the T&L industry across eight countries (U.S., Canada, Mexico, UK, Germany, France, Sweden and Australia), to understand the trends and solutions that are driving their organizations and how the pandemic affected operations.
Legacy Systems Not Integrated With New Investments Continue to Hinder Success and Result in Employees Losing Two Days of Work Per Month Due to Mobile Device Downtime
Despite this widespread investment in technology from T&L companies in 2020 and 2021, SOTI’s research indicated that this investment was not delivering the desired outcomes, with respondents suggesting that a lack of integration with existing systems is limiting productivity, creating siloed workflows and ultimately causing workers to lose valuable time when out in the field.
The delay due to mobile device downtime has led to 98% of global employees losing valuable work hours. Nearly one-third (32%) state that the main cause of downtime that cause shipping delays is the lack of IT support to address mobile device downtime issues, and self-serve applications that allow drivers to diagnose and troubleshoot device issues independently while they are on the road. On average, organizations are losing 3.3 hours per employee each work week dealing with technical or system difficulties (device downtime), with a global average of 14 hours lost per employee per month.
Average Downtime Around the Globe Among T&L Companies (Per Employee):
- Canada 17 hours per month
- U.S. 15 hours per month
- UK 15 hours per month
- Germany 15 hours per month
- Sweden 15 hours per month
- France 12 hours per month
- Mexico 11 hours per month
“The pandemic put a spotlight on the need for an integrated technology strategy,” said Shash Anand, VP of Product Strategy, SOTI. “While we are seeing a clear investment in technology from T&L companies, we are not seeing a cohesive strategy for the implementation of new tech to counteract the repercussions of the pandemic. It is crucial for T&L decision-makers to understand that by not taking these factors into account, their organizations are wasting time and leaving money and productivity on the table.”
Transportation and Logistics Companies Reliant on Pen and Paper Processes Making Errors
Once investments have been made, an even bigger cause of employee downtime is the lack of integration with existing systems. This creates inefficiencies, often causing employees to rely on paper-based processes, causing further inefficiencies and room for manual errors. The following examples were more frequently cited:
- 45% say staff are updating multiple systems manually
- 31% say legacy tech is not fully integrated with new systems
- 29% say that information is not shared across all systems used
When asked about the issues causing downtime and delaying shipments, T&L employees cited the following:
- Updated information is not automatically shared across all the systems used (28%)
- There is a lack of staff training on the usage of technology (26%)
- Systems are not upgraded frequently enough (24%)
“There is a clear disconnect from the technology that T&L companies recognize they need, to the seamless adoption into their existing infrastructure,” continued Anand. “With an integrated mobility and IoT management platform, T&L companies are not only able to increase speed, but also minimize costs and ensure transparency in the delivery channel..”
SC
MR

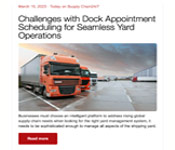
Latest Supply Chain News
Latest Podcast

Explore
Business Management News
- ‘Purple People’ and the evolution of supply chain talent
- Looking for the next frontier of margin enhancement? Think structurally
- ISM May Semiannual Report calls for growth in 2024, at a reduced rate
- Supply chain salaries top $100K for first time
- Supply chain’s rise in prominence brings regulatory compliance into focus
- Inflation continues to have a wide-ranging impact on supply chains
- More Business Management
Latest Business Management Resources

Subscribe
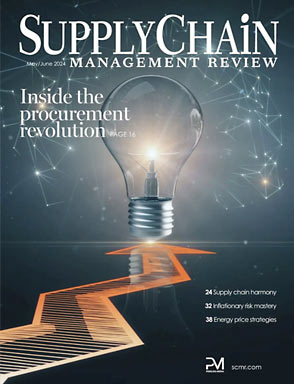
Supply Chain Management Review delivers the best industry content.
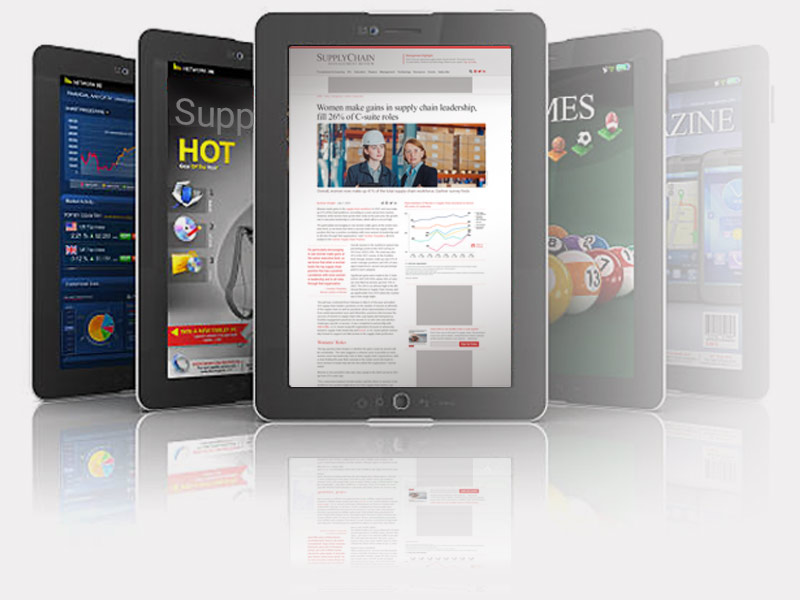
Editors’ Picks



