Sorry, but your login has failed. Please recheck your login information and resubmit. If your subscription has expired, renew here.
March-April 2024
Part of any supply chain manager’s job is risk mitigation. Thanks to COVID-19 and the ensuing, and constant, disruptions that have followed, more companies are now focused on reducing their exposure to supply chain chaos. We’ve heard a lot about diversification in recent years—having multiple suppliers in multiple locations. But risk mitigation goes far beyond diversification, and the recent case of Boeing should serve as a cautionary tale not to avoid those other risks. Browse this issue archive.Need Help? Contact customer service 847-559-7581 More options
Warehouse autonomous mobile robots (AMRs) are interactive robots leveraging advanced sensors and artificial intelligence (AI) to provide material handling capabilities within a confined area. The affordability, flexibility, and scalability of AMRs make them attractive solutions for increasing efficiency and effectiveness while reducing injuries and worker fatigue. Yet, the novelty of autonomous technology, humans sharing space with AMRs, and executing warehouse tasks collaboratively (e.g., order-picking) drive both excitement and anxiety when adopting such innovative, cutting-edge technology.
Integration of warehouse automation is a demanding task regardless of the type of technology; however, introducing AMRs into warehouse environments creates several unique challenges and complexities. Managing AMR integration projects to adequately address these challenges and complexities is critical to realizing the full potential of AMRs, and consequently, to achieving expected return on investments (ROI). In this article, we put forth a process framework for AMR integration and use in warehouses. This article leverages our research involving interviews with 17 professionals with hands-on experience with AMR integration projects from 14 different firms representing a variety of industries and roles.
The technology
Most warehouses employ manual, picker-to-part order-picking strategies. This approach, which relies on employees walking or driving to various warehouse locations to retrieve and deliver items to central processing locations, requires significant human capital investment. Not surprisingly, order picking has long been targeted by automation efforts seeking to increase efficiency and reduce human error. Automation solutions offer several benefits including reduced operational costs, greater warehouse utilization, increased order-picking accuracy, and shorter pick times. Yet, many small- and medium-sized firms forgo automating due to risks in upfront expenditure and loss in flexibility.
This complete article is available to subscribers only.
Log in now for full access or start your PLUS+ subscription for instant access.
SC
MR
Sorry, but your login has failed. Please recheck your login information and resubmit. If your subscription has expired, renew here.
March-April 2024
Part of any supply chain manager’s job is risk mitigation. Thanks to COVID-19 and the ensuing, and constant, disruptions that have followed, more companies are now focused on reducing their exposure to supply chain… Browse this issue archive. Access your online digital edition. Download a PDF file of the March-April 2024 issue.Warehouse autonomous mobile robots (AMRs) are interactive robots leveraging advanced sensors and artificial intelligence (AI) to provide material handling capabilities within a confined area. The affordability, flexibility, and scalability of AMRs make them attractive solutions for increasing efficiency and effectiveness while reducing injuries and worker fatigue. Yet, the novelty of autonomous technology, humans sharing space with AMRs, and executing warehouse tasks collaboratively (e.g., order-picking) drive both excitement and anxiety when adopting such innovative, cutting-edge technology.
Integration of warehouse automation is a demanding task regardless of the type of technology; however, introducing AMRs into warehouse environments creates several unique challenges and complexities. Managing AMR integration projects to adequately address these challenges and complexities is critical to realizing the full potential of AMRs, and consequently, to achieving expected return on investments (ROI). In this article, we put forth a process framework for AMR integration and use in warehouses. This article leverages our research involving interviews with 17 professionals with hands-on experience with AMR integration projects from 14 different firms representing a variety of industries and roles.
The technology
Most warehouses employ manual, picker-to-part order-picking strategies. This approach, which relies on employees walking or driving to various warehouse locations to retrieve and deliver items to central processing locations, requires significant human capital investment. Not surprisingly, order picking has long been targeted by automation efforts seeking to increase efficiency and reduce human error. Automation solutions offer several benefits including reduced operational costs, greater warehouse utilization, increased order-picking accuracy, and shorter pick times. Yet, many small- and medium-sized firms forgo automating due to risks in upfront expenditure and loss in flexibility.
SC
MR

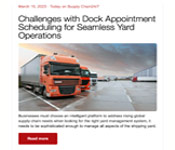
Latest Supply Chain News
- Three frameworks for creative problem-solving in supply chain
- Mitigating geopolitical uncertainty: 4 essential tactics for industrial CSCOs
- Supply chain strategy for medical devices: A Q&A with industry expert Sanjay Gupta
- Inventory Management and the Supply Chain: Outlook 2025
- How technological innovation is paving the way for a carbon-free future in logistics and supply chains
- More News
Latest Podcast
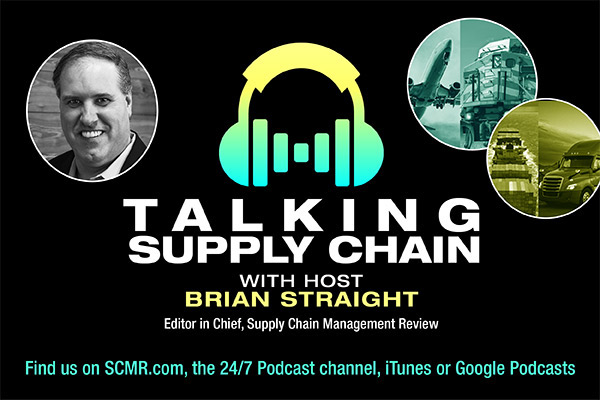
Explore
Software & Technology News
- How technological innovation is paving the way for a carbon-free future in logistics and supply chains
- Körber Supply Chain Software’s Craig Moore says MercuryGate acquisition is about the customer
- Robotic use grows by 10%
- Harnessing Edge Computing and AI Vision Systems for Real-Time Logistics Insights
- The art of winning at supply chain technology: Lessons from managing tech for the largest private trucking fleet in the U.S.
- The 3 types of cyberattacks affecting global supply chains
- More Software & Technology
Latest Software & Technology Resources

Subscribe
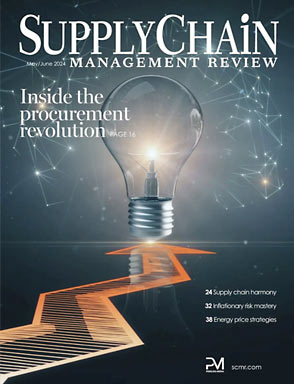
Supply Chain Management Review delivers the best industry content.
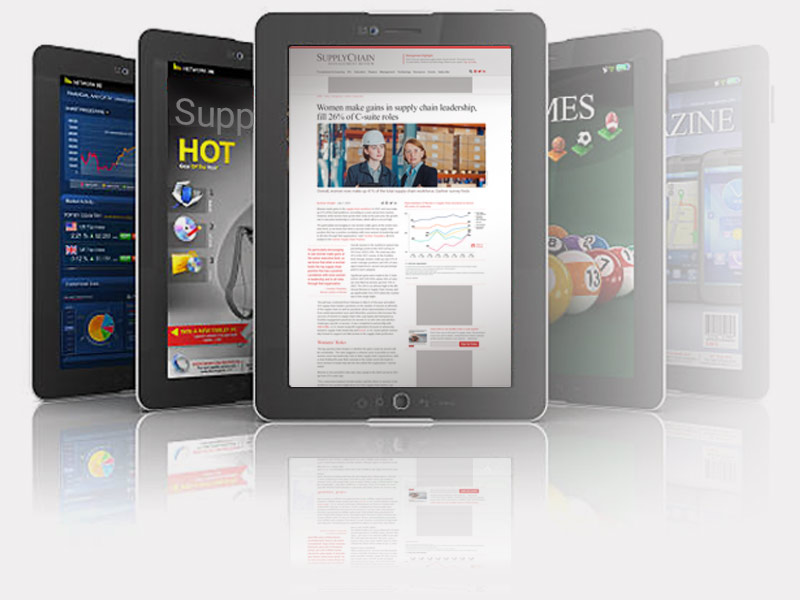
Editors’ Picks



