Editor’s note: This article by Francesco Stefanelli was originally published on July 25, 2017, and based on research the author did with Jim Rice, deputy director of MIT's Center for Transportation & Logistics. Their research suggested that the era of long, low-cost supply chains might be coming to an end as global supply chains would be redesigned into regional supply chains to serve local areas. It’s a topic that is much in the news today.
Without question, today's companies are global in nature. As such, they're exposed to uncertainty and volatility in the market, where the only certainty is that of the unavoidable and continuous mutation of the conditions under which they operate. For many companies, this translates into a dynamic environment when it comes to the design of their supply chains, leading many to locate manufacturing operations off shore.
More than 20 years ago, for instance, General Motors began moving its facilities into the Far East as part of a global supply chain. This helped elevate the supply chain in the development of a company's business. In more recent years, a number of factors have led some to claim that there is a groundswell of movement by companies to shutter offshore operations and re-shore them to the United States or Europe – wherever their Western headquarters are located.
Re-shoring has been much in the news, but it can be confusing. On the one hand, there are surveys like the one conducted in 2016 by AlixPartners which concluded that nearly 70 percent of U.S. and European manufacturing firms were considering moving production closer to their home bases. Similarly, in a report claiming that “the tide has turned,” the Reshoring Initiative noted that “Reshoring and [Federal Direct Investment] together were up over 10% in 2016, with much of the increase coming in November and December, presumably due to anticipation of greater U.S. competitiveness following the election.” The report also stated that more jobs were created from FDI than from reshoring, but that reshoring jobs increased at a higher rate greater at a higher rate than FDI from 2015 to 2016.
So far, so good. Yet, at the same time, news reports, while anecdotal, send mixed messages. Earlier this year, the Wall Street Journal published an article headlined “Firms Struggle to Bring Jobs Back,” detailing the challenges firms face “in sectors where the U.S. ecosystem of manufacturers, suppliers and skilled workers has largely disappeared.” Meanwhile, companies such as Carrier and Ford have recently announced plans to launch new manufacturing capacity in Mexico and China respectively.
Indeed, just this week came a report that more U.S. cars are being manufactured in Mexico than ever. “The data indicates one in five cars built in the North American Free Trade Agreement zone comes from Mexico, including hot new products from General Motors Co. and Fiat Chrysler Automobiles NV. That is up from the industry's reliance on Mexico during the financial crisis, when the U.S. car business received billions of dollars in bailouts aimed at preserving jobs and keeping domestic players afloat.”
If all of that sounds confusing to you, you're not alone. What then is going on? In order to better answer that question, this author and Jim Rice, deputy director of MIT's Center for Transportation & Logistics, developed a cross-industry quantitative model, referring to the United States and China as the final marketplace and as the global production place, respectively.
Through the model, the study was able to summarize how re-location key-factors developed in a timespan from 1999 to 2012, taking the American market as the final reference point, and considering the Chinese baseline as a production reference. We also examined how industry cost structures evolved during that same period. An analysis of the data allowed us to study several related trends. Our conclusions were in contrast to a broad set of surveys that have emerged from many trade article magazines.
The most relevant is as follows: “there is no reshoring at all,” at least when the phenomenon has been defined as the re-location of production capacity from low cost countries back to the United States. In fact, our study argues that reshoring is not far enough along to be considered quantitatively relevant. Rather, we concluded that what is described as re-shoring activity may have more to do with broader supply chain changes than a revitalization of American manufacturing. While the end point for the data was 2012, this author believes that broader supply chain changes are still the determining factor as to why companies locate their manufacturing in one locale over another.
For instance, while some industries were relocating production back to the U.S. during that period, other sectors continued to move off-shore. What's more, the most notable trend we identified was that of global companies shifting their supply chain structures from global to regional ones - that is they were moving in order to optimize supply chain structures on a global scale. By adopting a “back home strategy,” global companies are actually shifting their supply chains from centralized to regional structures that locates production closer to consumption.
Being closer to the customer allows companies to adapt to changes in the market and consumer demand in a shorter time, optimizing and fixing key-changes about critical issues related to industry cost structures' factors. The phenomenon of Foreign Direct Investment, in which a foreign entity launches manufacturing activity in the United States, is often included in re-shoring activity, but this author would argue that it is more representative of a restructuring of supply chains to get closer to the customer than of re-shoring.
The cost of labor is a good example. During the time period we studied, there was a considerable increase in productivity that made the cost of labor in the US particularly attractive, especially because the cost of labor in China increased too. For instance, our research found that U.S. labor costs related to consumer appliances, machinery and furniture decreased about 9%, 6% and 4% respectively. Assuming a similar Chinese structure as counterpart of the American one, the overall cost gap between US and China has been reduced so that some manufacturing activities might be relocated back in US. Yet, at the same time, the wage gap between the US-China apparel and fashion industries increased by 8%.
In addition, the effects of the unpredictability of the price of crude oil contributes to a fluctuation in the structure of some industry costs, especially where the cost of transportation assumes a key role in the business. In the consumer appliances and furniture's industries, related transportation cost ratios might affect up to 20% of the cost, due to oil fluctuation: hence, oil price variability might mean whole cost structure instability.
Rather than looking at re-shoring as a trend, the authors see it as a strategic option to pick whenever the related industry cost structure's conditions push to a different business model, making production closer to consumption to a “local-to-local” approach that allows firms to better serve the customer.
Francesco Stefanelli, Ph.D., is a supply chain manager and a former visiting researcher at MIT's Center for Transportation & Logistics. He can be reached by email at [email protected].
SC
MR
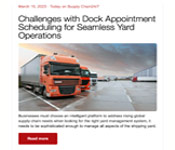
Latest Supply Chain News
Latest Resources

Explore
Topics
Latest Supply Chain News
- Supply chain salaries top $100K for first time
- Supply chain’s rise in prominence brings regulatory compliance into focus
- Inflation continues to have a wide-ranging impact on supply chains
- A reshoring history lesson
- Strategic cost savings differ from cutting costs
- Planning fatigue may be settling in
- More latest news
Latest Resources

Subscribe
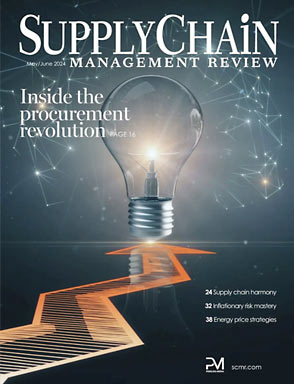
Supply Chain Management Review delivers the best industry content.
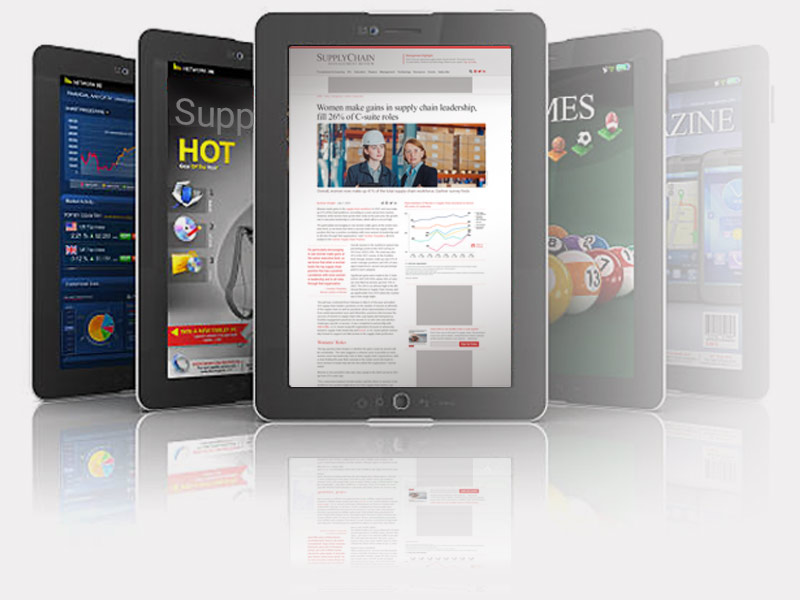
Editors’ Picks



