Back in May of 2015, I published an article on additive manufacturing out of the University of Louisville, where they have an extensive additive manufacturing lab. The sense three years ago was that 3D printing had found a niche in specific areas, such as prototyping, the dental industry and service parts or parts with a low demand. But there was also much work to be done for 3D printing to become a viable option to conventional manufacturing, especially parts produced in the thousands.
Three years, of course, is a lifetime in technology. A conversation I had with Stuart Pann, the chief supply chain officer at HP, provided a glimpse into just how far 3D printing has come since that article.
Now, HP is a leading provider of 3D printing technology, so you might be tempted to think: Well, of course HP is bullish on 3D printing. But Pann is a supply chain executive and not a marketing executive. His job, in part, is to make sure the best parts are available to HP manufacturing partners, like Jabil, to keep the manufacturing lines running as efficiently and cost-effectively as possible. He also brings a unique perspective to the task, which is the 33 years he spent at Intel. He began our conversation with a reference to Moore's Law, “the observation that the number of transistors in a dense integrated circuit doubles about every two years.”
“An HP digital printer puts tiny drops of ink through tiny nozzles at high speed,” Pann said. “When the first ink jet printer came out more than 30 years ago, it would print something like 10,000 drops per second. Today, our largest format printers might have 20,000 nozzles firing and we're up to a couple of billion drops per second. If you graph that over time, it's a Moore's Law kind of progression, doubling the number of drops every 18 to 24 months.”
He added that something similar is happening with 3D printers, which in HP's case use technology similar to ink jet printing to lay down layers of material and fusing agents. “We have 30 years of IP and investment into technology to lay down drops and no one else can do it at that level,” Pann said. He added that since there are no molds or tooling “you get complexity for free, which means you can print things you could never do in injection molding or a CNC machine,” Pann said.
But, does it make economic sense to use 3D printing for full production (what we're now going to call digital manufacturing), versus conventional injection mold manufacturing, (what we'll now call analog manufacturing)? Especially if you need to produce tens of thousands of parts?
The answer, based on HP's experience since launching its “Reinventing HP with Multi Jet Fusion” program earlier this year – and also that pesky Moore's Law – is a resounding yes, but in the right application. Pann says he challenged his staff to look at the technology purely from a supply chain perspective, and identify those parts that could be manufactured digitally by Jabil, with clear advantages over doing so by traditional methods, and do so objectively, without putting their thumbs on the scale in favor of HP's 3D technology. Yes, he wanted to leverage the benefits HP's technology, but only if it delivered new value compared to an analog process. His expectations were low: “I thought we'd find three or four parts that made sense.”
As it turned out, more than 140 parts were candidates in one product alone, HP's new Jet Fusion 300/500 series full-color 3D printers, representing 50 percent of the plastic parts in each unit. In part, that was the case because the volume of the parts needed was relatively low; some of the biggest savings were realized because no tooling was required, cutting manufacturing and assembly times and production costs dramatically.
That volume thing, however, is changing too, and it's beginning to look like another Moore's Law progression. As the cost of materials comes down, the cost per part is also coming down. Today, the break-even point has been raised to 110,000 parts - above that and you can spread the cost of tooling across enough parts to make injection molding a cheaper alternative. But, in the not so distant future, Pann expects that to grow much further. “We're moving from high-complexity, low-volume parts to lower-complexity, higher-volume parts,” he said. He envisions a time when the break-even will be a million parts.
I asked Pann for his advice to other supply chain executives looking to go digital. He suggests beginning with parts that require a lot of hard tooling, but also have a quick time to market. “If you have to make a mechanical change, there's no tooling charges for a 3D printed part,” he said. Other potential candidates are parts purchased in quantities of tens of thousands for products with a long lifecycle. The reason: You'll always have the digital file to create service parts that are identical to the original down the road. Finally, he suggests looking at complex components that involve multiple parts that are screwed or fastened together. “With 3D printing, you may be able to design a component that can be printed complete as a single part,” he says.
What doesn't work? “If you're making millions of units a year and buying super cheap resins, that's not a 3D printing application,” he said, adding that in some industries and applications, especially those with small volumes, 3D manufacturing is already here. “Jabil, our manufacturing partner, is already building out full 3D manufacturing network,” he said.
SC
MR

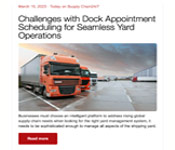
Latest Supply Chain News
- Few executives believe their supply chains can respond quickly to disruptions
- Technology’s role in mending supply chain fragility after recent disruptions
- Tech investments bring revenue increases, survey finds
- Survey reveals strategies for addressing supply chain, logistics labor shortages
- Israel, Ukraine aid package to increase pressure on aerospace and defense supply chains
- More News
Latest Podcast
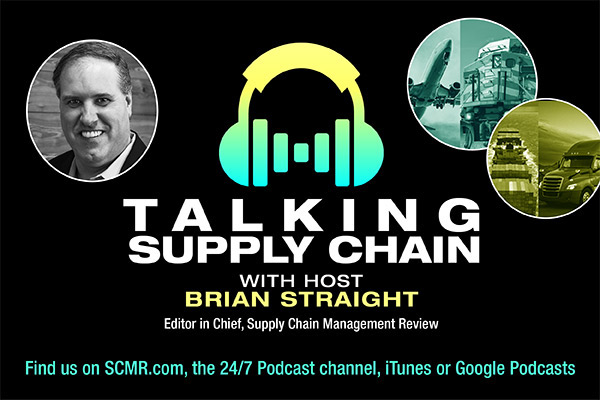
Explore
Topics
Latest Supply Chain News
- Few executives believe their supply chains can respond quickly to disruptions
- Technology’s role in mending supply chain fragility after recent disruptions
- Tech investments bring revenue increases, survey finds
- Survey reveals strategies for addressing supply chain, logistics labor shortages
- Israel, Ukraine aid package to increase pressure on aerospace and defense supply chains
- How CPG brands can deliver on supplier diversity promises
- More latest news
Latest Resources
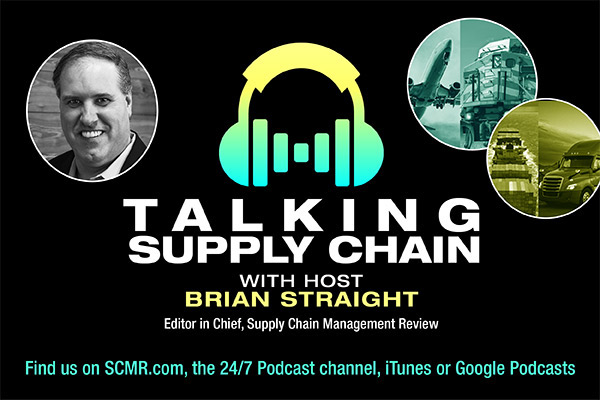
Subscribe
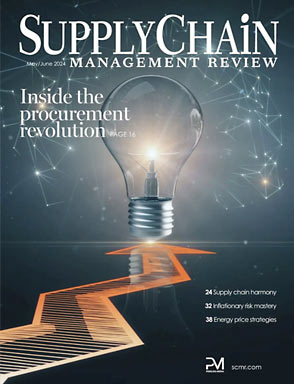
Supply Chain Management Review delivers the best industry content.
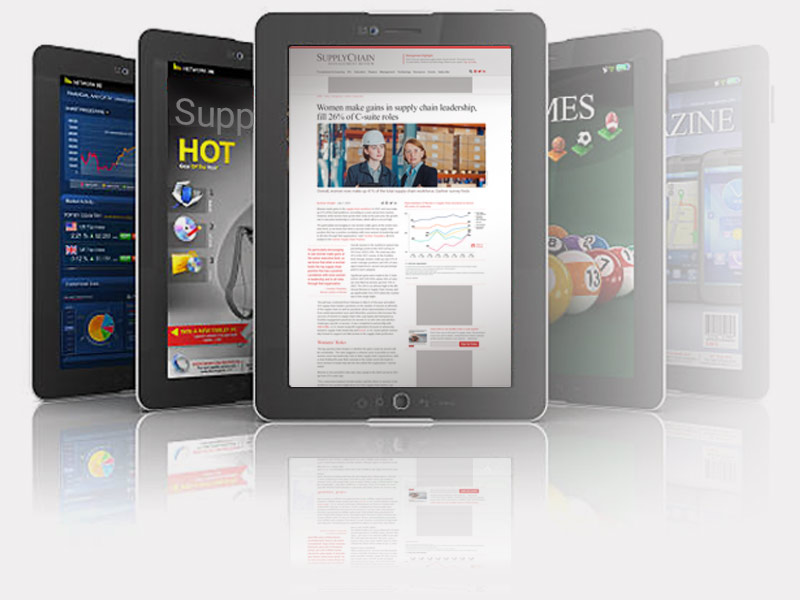
Editors’ Picks



