Supply Chain Risk Can Manifest in Devastating Ways
Global supply chains are a source of competitive advantage. They provide access to inexpensive labor and raw materials, better financing opportunities, larger product markets, arbitrage opportunities, and additional inducements offered by host governments to attract foreign capital. However, coupled with these benefits that entice firms to go global are the uncertainties and consequent risks that global supply chain managers must face.
Since the life blood of the corporation flows through its supply chain, any changes to it can carry huge risk. Supply chain disruptions can result in a devastating impact on shareholder value; with one study showing an average 40 percent decline in share price due to the supply chain disruptions in the study. The lack of a risk-management process is especially evident with global outsourcing initiatives.
For example, a dishwasher manufacturer told us that they decided to outsource the production of water seals to China. The net savings considering all known costs was nearly $0.75 per unit and totaled a $2 million annual savings. But soon after the arrangement was made, the Chinese supplier changed to a different rubber supplier, resulting in a catastrophic problem. The seals made from this new rubber were found to leak in dry climates, causing nearly a 10 percent failure rate. Before the problem was discovered, over two million dishwashers had been produced with the defective seal. When the seal failed, and the unit leaked water onto the kitchen floor, it took an average cost of $125 to fix, which included some compensation for water damage to kitchen floors to maintain goodwill and to try to salvage some of the manufacturer’s reputation. The total cost to the company, once the dust settled, was north of $7 million. This one event wiped out savings from the outsourcing initiative for over three years! The company thought they had taken all factors into consideration. But they failed spectacularly in considering the potential risks.
Only 10 Percent Consider Risk When Outsourcing Clearly, it is extremely important that a supply chain outsourcing strategy identify risks, and that the change-management plan appropriately mitigates those risks. However, when companies analyze global outsourcing decisions, we find that they fall into three categories:
- Category One (35 percent): Look at unit cost plus transportation cost only
- Category Two (55 percent): Include inventory cost as part of the assessment
- Category Three (10 percent): Add a risk assessment
Supply Chain Risk is Also a Local Phenomenon
It’s not just the global environment that creates supply risk. There’s plenty of it in almost every major initiative. For example, a supply chain professional from a retailer specializing in children’s toys told of trying to implement a new fulfillment system that was completed months late and far over and budget. The Christmas spike exploded before the fulfillment system was complete, resulting in an inability to process orders. People throughout the company worked 50 days straight, including Sundays, to try to stay ahead, yet the firm was forced to send thousands of letters saying, “Sorry your toy order will not arrive before Christmas.”
In another alarming example, a candy maker spent over $100 million installing a new supply chain decision support system. The “go-live” for this project slipped from April to September. As the Halloween spike approached, the firm pushed the system into operation before it was ready and subsequently missed $150 million of sales due to an order processing process containing many bugs. The stock dropped 45 percent. In yet another situation, a shoe manufacturer installed a complex new system to run its supply chain. Again, there were major delays. The company’s CEO announced that there would be a $100 million sales shortfall due to this new software, causing the stock to fall 20 percent.
Identifying, and Prioritizing Risk
Supply chain risk, of course, cannot be managed unless it is first identified and prioritized. Companies need a standard process for doing that, and the examples below illustrate two such approaches.
Engineers long ago developed a well-known approach to identify and prioritize risks using the FMEA (failure mode and effects analysis) approach. The military has used the FMEA approach as far back as the 1940s. Those familiar with it know that it prioritizes risks based on three factors:
1. Seriousness of consequences
2. Likelihood of the problem ever occurring, or frequency of occurrence.
3. Likelihood of early detection of the problem
We know of several firms that have successfully applied this approach to supply chain issues as a way of identifying high-priority risks that would then require a mitigation plan. They tell us that the framework serves as a vehicle to guide the discussion of risks in a group setting; and that’s the real power of it. Given that risk analysis has a large subjective component, reaching group consensus is critical.
Addressing Supply Chain Risk at a Food Manufacturer A food products manufacturer planned to outsource its warehouse operations to a third party. It used a table similar to the one below to guide the risk discussion. Its supply chain group, in brainstorming sessions, identified 13 risks. Using the approach below, the company prioritized these risks and eventually decided to launch a mitigation project for the top five prioritized risks. An example using just two of the identified risks is shown in Table 1 below:
Risk 1: Safety of Food Product |
Risk 2: Freshness of Product |
|
Severity (1-10) |
9 | 6 |
Probability of Occurrence (1-10) |
2 | 4 |
Probability of Early Detection |
6 | 2 |
Probability Index (Multiply Three Items Above |
9 x 2 x 6 = 108 | 6 x 4 x 2 = 48 |
Recommended Action |
Enhance testing process | Audit inventory, and ensure stock rotation |
Responsibility |
Safety engineering | Third party with company oversight |
There are other examples, especially with defense contractors, who have quite sophisticated approaches to managing risk, even using stochastic simulations. Sadly, even simplistic risk management approaches are exceptions. The vast majority of firms have no formal process at all for dealing with supply chain risk. Yet, the supply chain essentially determines the overall financial health of the firm. Because of that, any risk magnifies in importance. It is essential that firms have a disciplined process in place to identify, prioritize, and manage the wide range of risks that can impact their supply chain.
SC
MR
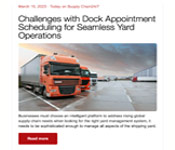
Subscribe to our weekly e-mail update
Don’t miss out on the best in supply chain. Latest Supply Chain News
- Looking for the next frontier of margin enhancement? Think structurally
- ISM May Semiannual Report calls for growth in 2024, at a reduced rate
- Augmented reality’s role in upskilling the workforce
- Supply chain salaries top $100K for first time
- Supply chain’s rise in prominence brings regulatory compliance into focus
- More News
Latest Podcast

Talking Supply Chain: Why a Stanley cup can disrupt the supply chain
When a special Valentine’s Day-theme Stanley tumbler went viral, it caused a surge in product sales, highlighting the challenges the supply…
Explore
Topics
Latest Supply Chain News
- Looking for the next frontier of margin enhancement? Think structurally
- ISM May Semiannual Report calls for growth in 2024, at a reduced rate
- Augmented reality’s role in upskilling the workforce
- Supply chain salaries top $100K for first time
- Supply chain’s rise in prominence brings regulatory compliance into focus
- Inflation continues to have a wide-ranging impact on supply chains
- More latest news
Latest Resources

Talking Supply Chain: Why a Stanley cup can disrupt the supply chain
When a special Valentine’s Day-theme Stanley tumbler went viral, it caused a surge in product sales, highlighting the challenges the supply…
Subscribe
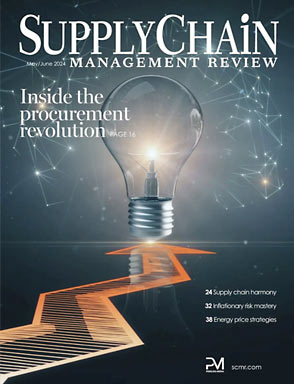
Supply Chain Management Review delivers the best industry content.
Subscribe today and get full access to all of Supply Chain Management Review’s exclusive content, email newsletters, premium resources and in-depth, comprehensive feature articles written by the industry's top experts on the subjects that matter most to supply chain professionals.
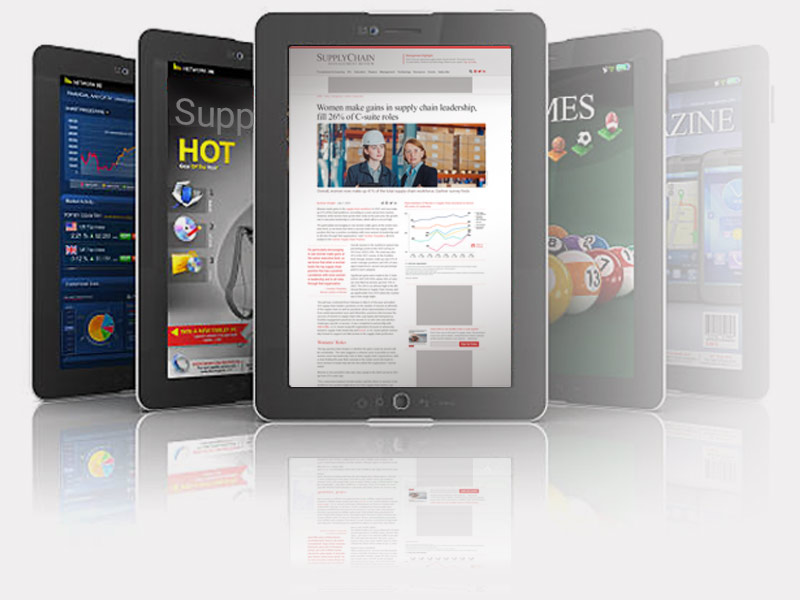
Editors’ Picks

Port of Baltimore May Not Reopen Until Summer
The Port of Baltimore may remain closed until at least May, and possibly into…

A New Priority Greets Procurement Professionals in 2024
Cost reduction supplants supply continuity as the top issue facing…

Supply Chains Facing New Pressures as Companies Seek Cost Savings
A Boston Consulting Group survey of global executives found a majority are…

Digital Approaches, End-to-End Thinking Help Supply Chains Evolve
Supply chain disruptions come in many forms, but digital approaches and…
© Copyright 2024 Supply Chain Management Review, a division of Peerless Media. All Rights Reserved.
×