Sorry, but your login has failed. Please recheck your login information and resubmit. If your subscription has expired, renew here.
September-October 2014
2014 marks the 10 year anniversary of the Gartner Supply Chain Top 25 ranking. This year we have a diverse set of large, global companies with mature, demand-driven supply chains. There are lessons to be learned from these supply chain leaders, many of whom have led their industries over the past decade. Browse this issue archive.Need Help? Contact customer service 847-559-7581 More options
When it came, the sign that something was wrong with one of Intel’s supply chains was not hard to miss. A key subcontractor for a particular Intel business unit was awash in excess inventory for turnkey and consigned parts. The cause? Someone had wrongly entered the required order quantity, and the subcontractor had acted on that information.
But that was simply the manifestation of the problem. The real problem was that nobody caught the problem until it was much too late—until this particular business unit (BU) owned the parts its subcontractor had unwittingly ordered. Nobody caught it because nobody knew about it: The BU had no proactive way of identifying, let alone cross-checking, appropriate purchases against actual demand. It did not have visibility.
What went wrong? That is a question those of us with supply chain responsibilities have examined at Intel reaching back at least to 2009, when my team identified a collaboration supply chain software program to address our outsourcing challenges. While putting this solution in place had to wait until a corporate-wide software initiative was well underway, rolling it out ultimately involved a broad training and certification program for supply chain planners, buyers, and managers. Along with raising the skill level and supply chain knowledge of our team, it set the stage for the collaborative pilot program that is currently in place with our partners. What follows are the steps of how we did it at Intel.
![]() |
This complete article is available to subscribers
only. Click on Log In Now at the top of this article for full access. Or, Start your PLUS+ subscription for instant access. |
Not ready to subscribe, but need this article?
Buy the complete article now. Only $20.00. Instant PDF Download.
Access the complete issue of Supply Chain Management Review magazine featuring
this article including every word, chart and table exactly as it appeared in the magazine.
SC
MR
Sorry, but your login has failed. Please recheck your login information and resubmit. If your subscription has expired, renew here.
September-October 2014
2014 marks the 10 year anniversary of the Gartner Supply Chain Top 25 ranking. This year we have a diverse set of large, global companies with mature, demand-driven supply chains. There are lessons to be… Browse this issue archive. Access your online digital edition. Download a PDF file of the September-October 2014 issue.
![]() |
Download Article PDF |
When it came, the sign that something was wrong with one of Intel’s supply chains was not hard to miss. A key subcontractor for a particular Intel business unit was awash in excess inventory for turnkey and consigned parts. The cause? Someone had wrongly entered the required order quantity, and the subcontractor had acted on that information.
But that was simply the manifestation of the problem. The real problem was that nobody caught the problem until it was much too late—until this particular business unit (BU) owned the parts its subcontractor had unwittingly ordered. Nobody caught it because nobody knew about it: The BU had no proactive way of identifying, let alone cross-checking, appropriate purchases against actual demand. It did not have visibility.
What went wrong? That is a question those of us with supply chain responsibilities have examined at Intel reaching back at least to 2009, when my team identified a collaboration supply chain software program to address our outsourcing challenges. While putting this solution in place had to wait until a corporate-wide software initiative was well underway, rolling it out ultimately involved a broad training and certification program for supply chain planners, buyers, and managers. Along with raising the skill level and supply chain knowledge of our team, it set the stage for the collaborative pilot program that is currently in place with our partners. What follows are the steps of how we did it at Intel.
![]() |
SUBSCRIBERS: Click here to download PDF of the full article. |
SC
MR
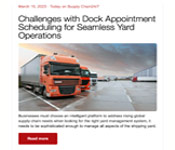
Latest Supply Chain News
- Despite American political environment, global geopolitical risks may be easing
- Joseph Esteves named CEO of SGS Maine Pointe
- Employees, employers hold divergent views on upskilling the workforce
- April manufacturing output slides after growing in March
- Q1 sees a solid finish with positive U.S.-bound import growth, notes S&P Global Market Intelligence
- More News
Latest Podcast

Explore
Latest Supply Chain News
- Despite American political environment, global geopolitical risks may be easing
- Joseph Esteves named CEO of SGS Maine Pointe
- Employees, employers hold divergent views on upskilling the workforce
- April manufacturing output slides after growing in March
- Q1 sees a solid finish with positive U.S.-bound import growth, notes S&P Global Market Intelligence
- World Trade Centers offers a helping hand to create resilient, interconnected supply chains
- More latest news
Latest Resources

Subscribe
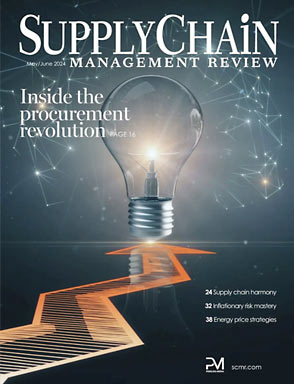
Supply Chain Management Review delivers the best industry content.
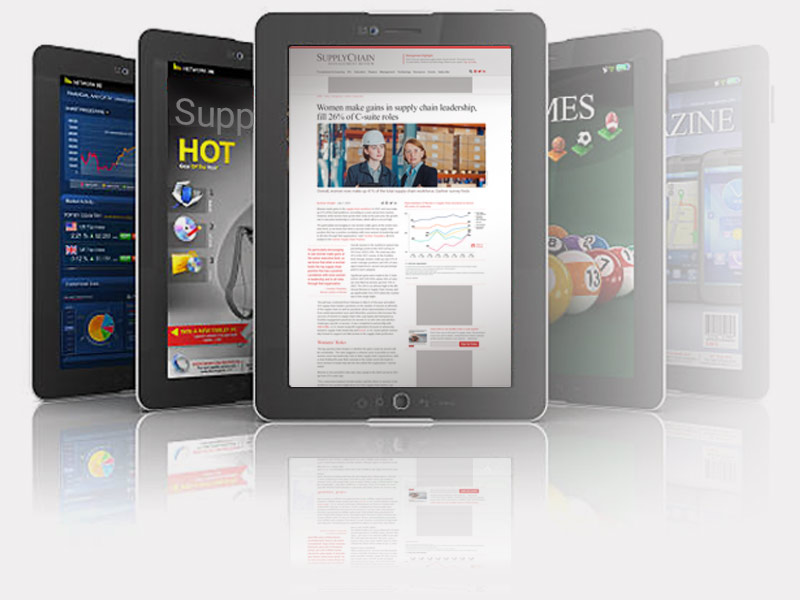
Editors’ Picks



