“I get excited when someone says to me: ‘I have 17 trailer loads of excess product,’” says Claudia Freed.
Excess inventory may not be your everyday conversation starter, and it’s not every day that you find an individual who gets excited by the topic. But then Freed is the CEO and president of EALgreen, which is not your everyday philanthropic organization.
The EAL stands for Educational Assistance Limited. The organization was founded some 40 years ago to provide a means for manufacturers and distributors to earn a tax credit by donating excess inventory to fund college scholarships. Freed, who joined EALgreen as executive director in 1995, was the recipient of the first scholarship in 1982. Back then, she was an immigrant student who had come to the states from Argentina as an 18-year-old with $36 in her pocket. “When I received the scholarship, I was a student at North Park University studying economics, and someone deemed that I had potential,” she recalls. Funding students with potential remains the social impact part of the mission today.
I came across EALgreen in a press release after the organization was awarded the Green Logistics Award by the Reverse Logistics Association. RLA noted that EALgreen was the first non-profit recognized for sustainability and that it had shown “great leadership in sustainable reverse logistics operations with an innovative alternative for returns, excess and end-of-life inventory that results in less waste and eco-impact.”
Freed describes what the organization does as “product philanthropy.” The operational objective is to avoid waste in all its forms. Part of that is looking for ways to reuse, repurpose or recycle the excess inventory it receives, or, in the alternative, auctioning it off to a third party. And, part of that is transporting and processing that inventory in the most sustainable way.
To that end, EALgreen operates two distribution centers: One in Rockford, Illinois and the other in Southern California. Between them, the two facilities process between 500 and 700 trailer loads of donated product a year. On the logistics side, the organization recruited a transportation expert two years ago to set up an inhouse transportation department. “The way we move product into our warehouses is the E in ES&G,” Freed says. “We are constantly looking at shipping rates, lanes and backhauling opportunities. We minimize miles by using a lot of intermodal transportation and empty miles by backhauling whenever possible.”
Priorities are given to product that can be used to run a college or university campus – that could be everything from lab equipment to lawnmowers to acoustic ceiling tile. In fact, EALgreen has a deal with Armstrong, which uses tiles that are beyond their usable life to make recycled ceiling tiles. “We don’t get money for that, but we advance the green,” says Freed.
The lists of items not accepted includes perishable products, although the organization can direct donors to food banks; hazardous materials; anything with a license plate that has been titled to an owner, like cars and boats; real estate; or items from outside the U.S.
Once product is received in a DC, it’s inspected to see if it can be used by a college. A lawnmower in working order would fit that bill and go on the website for sale. If it fails that test, it may be eligible for a repair channel; repurposed to another charitable organization; or sold and converted to cash. If it fails those tests, it can be recycled. That may also generate some cash.
The S is the social impact of EALgreen’s operations. Corporate donors receive an enhanced tax donation for their inventory. Meanwhile, colleges and universities join EALgreen’s network for free and gain access to the website. There, they can purchase product for a handling fee of about 10 cents on the dollar that helps cover the cost of logistics. The difference between the value of the product and the handling fee is converted into a discount on a worthy student’s tuition bill. “Instead of paying $100, they’re paying $10, and the $90 difference goes to reduce tuition,” says Freed. Last year, those savings funded average assistance of about $2,300 to 1,100 students nationwide. Since its founding, EALgreen has assisted over 21,000 students since the organization was founded.
Students are chosen by the universities and not the organization. “We want to empower financial directors of our partner colleges,” she says. Participating educational institutions are required to report their contributions to students back to the organization.
One important measure of effectiveness is how well a non-profit uses the money it raises. EALgreen’s income comes from the handling fees paid by its partner institutions; from product that is sold into other channels, such as auctions and liquidators; and from product it is able to recycle for cash – another best practice, like transportation and logistics, that the organization has developed. According to Freed, EALgreen keeps just 13% of the money generated from its operations and donates 87%. “At the end of the year, anything above and beyond a 6-month operating reserve is returned to colleges and universities in the form of a cash donation to their scholarship budgets,” she says. Last year, that amounted to $1,250,000, and $6 million over the past ten years.
“Our goal is to reduce waste in business and empower people with college degrees,” Freed says. And maybe that explains why she gets excited by 17 trailer loads of someone else’s excess inventory.
SC
MR
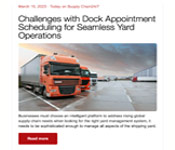
Latest Supply Chain News
- Despite American political environment, global geopolitical risks may be easing
- Joseph Esteves named CEO of SGS Maine Pointe
- Employees, employers hold divergent views on upskilling the workforce
- April manufacturing output slides after growing in March
- Q1 sees a solid finish with positive U.S.-bound import growth, notes S&P Global Market Intelligence
- More News
Latest Podcast

Explore
Topics
Latest Supply Chain News
- Despite American political environment, global geopolitical risks may be easing
- Joseph Esteves named CEO of SGS Maine Pointe
- Employees, employers hold divergent views on upskilling the workforce
- April manufacturing output slides after growing in March
- Q1 sees a solid finish with positive U.S.-bound import growth, notes S&P Global Market Intelligence
- World Trade Centers offers a helping hand to create resilient, interconnected supply chains
- More latest news
Latest Resources

Subscribe
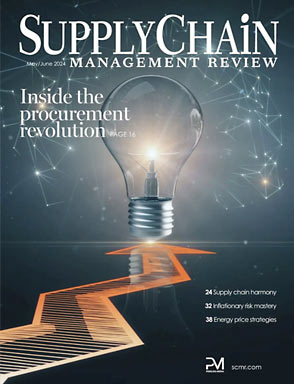
Supply Chain Management Review delivers the best industry content.
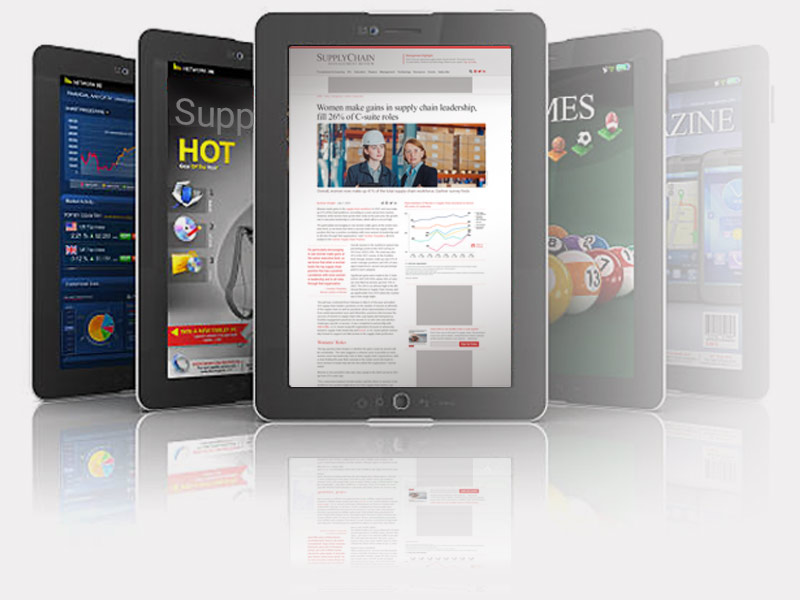
Editors’ Picks



